Speakers
Keynote Speakers
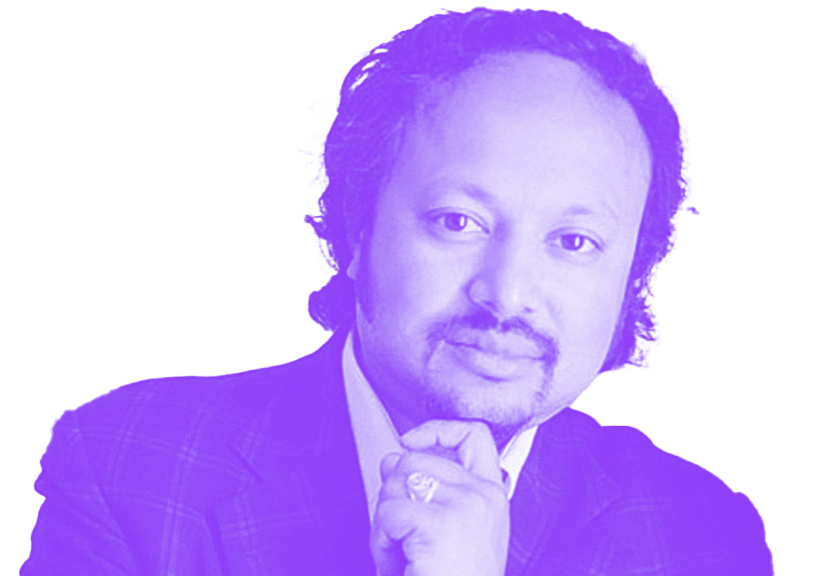
Anirban Basu
CEO & Founder
Sage Policy Group, LLC
Economist Anirban Basu, chairman and CEO of Sage Policy Group, in Baltimore, Maryland, returns to World of Modular to deliver an engaging economic forecast for the commercial modular construction industry. Since joining MBI as chief economist in 2022, Dr. Basu has provided consulting for various clients, including developers and law firms, and authored notable reports, such as MBI’s “Economic and Financial Performance of Relocatable Buildings in the US Modular Building Industry."
Sponsored By
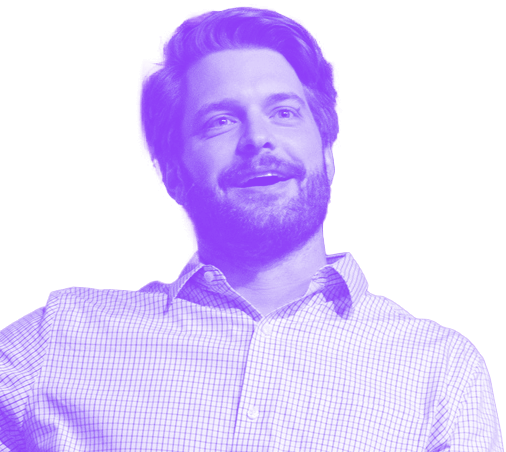
Kyle Scheele
Creativity & Innovation Expert
Author of “How to Host a Viking Funeral”
If there’s one belief holding you back from getting the most out of your team, it’s this: “some people are creative, and some aren’t.” Kyle contends that mindset is outdated. In reality, creativity is a skill anyone can learn—just like tracking expenses or processing invoices. Kyle will show you how to transform yourself and your organization into an innovation machine, offering practical tips to generate more and better ideas, explaining the 5 essential elements of every idea, and helping you avoid common idea-killers in the workplace.
Breakout Sessions
Spanning all four days of the conference, attendees can choose from dozens of educational breakout sessions covering distinct aspects of the commercial modular construction industry.
Follow Us for the Latest Updates
Follow us on LinkedIn to be the first to know about new session topics, featured speakers, and exciting announcements for World of Modular 2025. Stay connected for all the latest updates!
Breakout Speakers Include
The 2025 World of Modular will feature dozens of expert speakers from around the world. Check back often for updates!
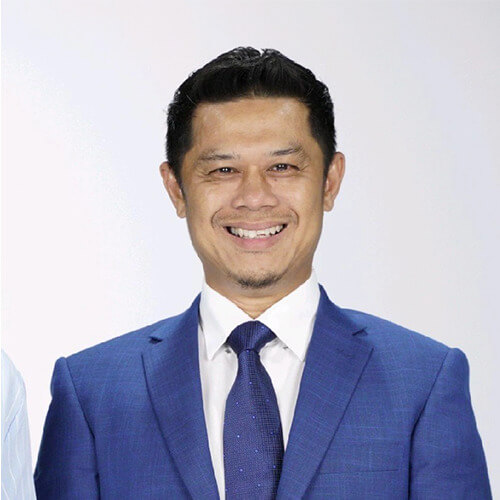
Rofizlan bin Ahmad
Senior General Manager
Construction Industry Development Board
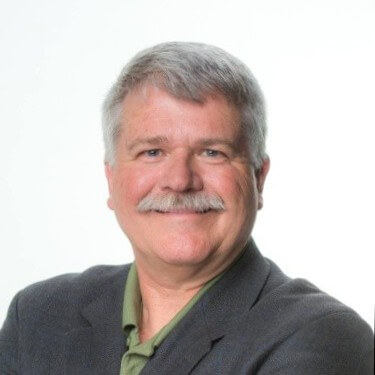
Sam Albrecht
Director, Office of Regulatory Oversight
Colorado
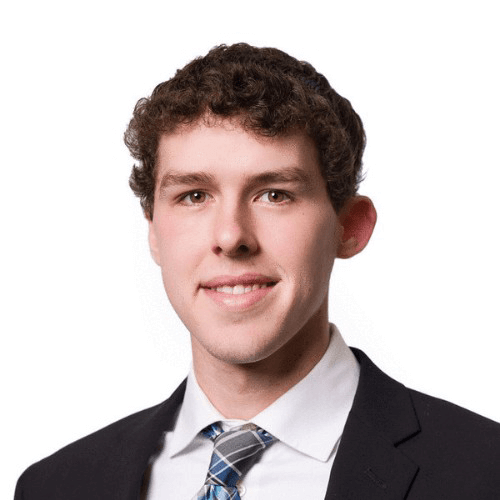
Vincent Armstrong
Business Development Manager
Avient
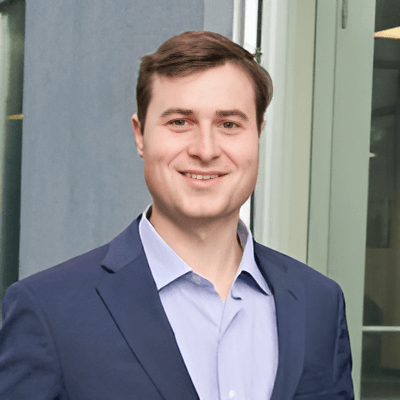
Trey Aucoin
Director of Operations
Marex Road Services, LLC
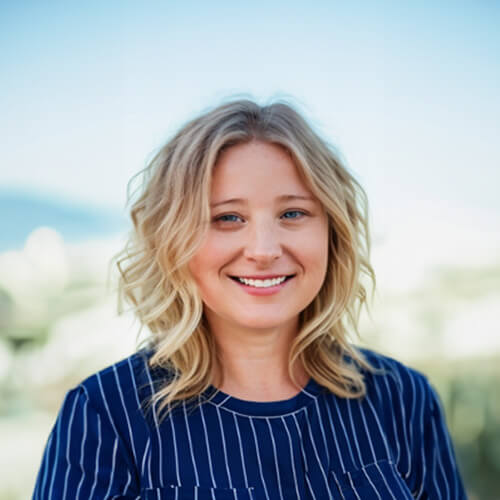
Callie Bailey
Studio Director
ASSEMBLAGEworks
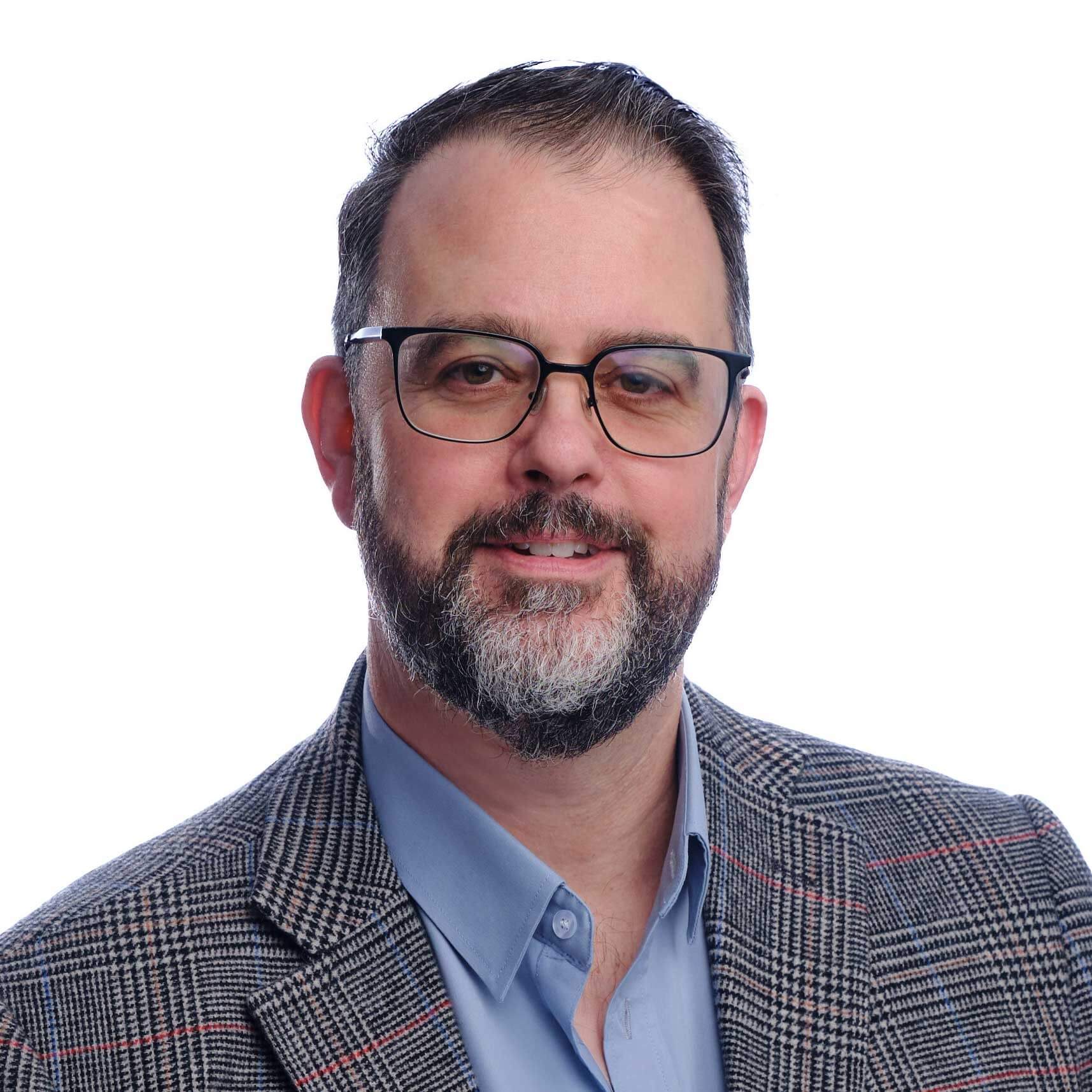
Geoff Baker
VP Strategy
Stack Modular
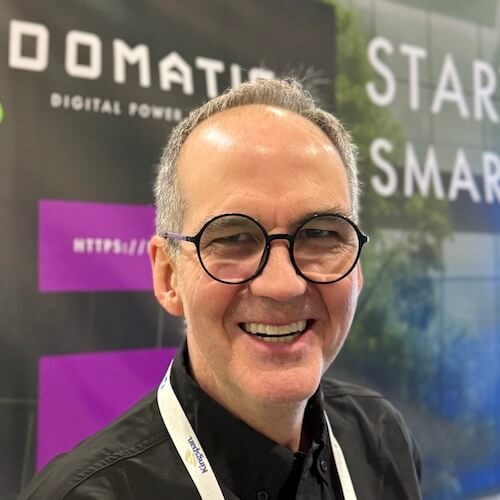
Jim Baldwin
CEO
Domatic
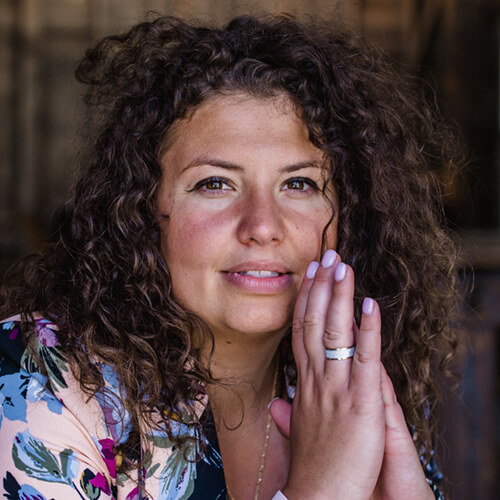
Pamela Bardhi
CEO
Revelution Group
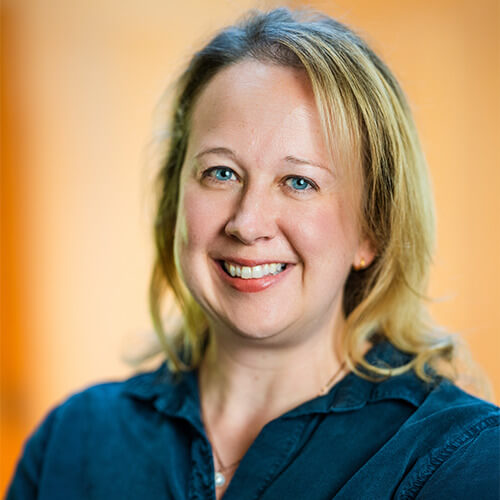
Emily Benson
Employee Success Officer
Bensonwood
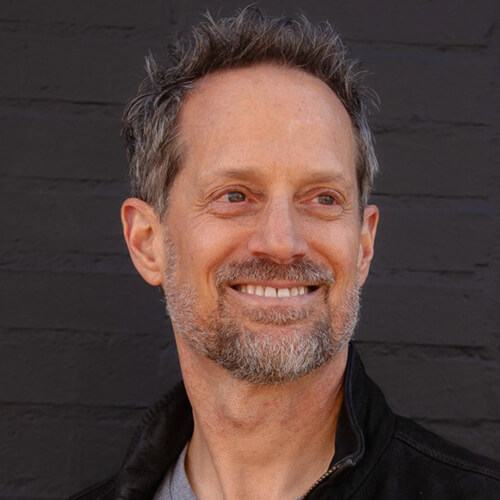
Adam Berger
Owner/Developer
Adam Berger Development, LLC
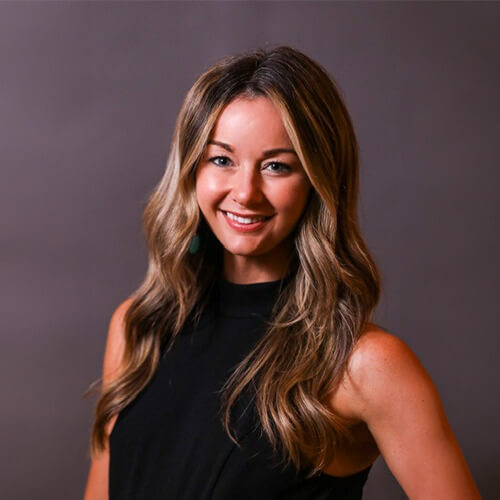
Sara Betancourth
Senior Manager and Counsel
AIA Contract Documents
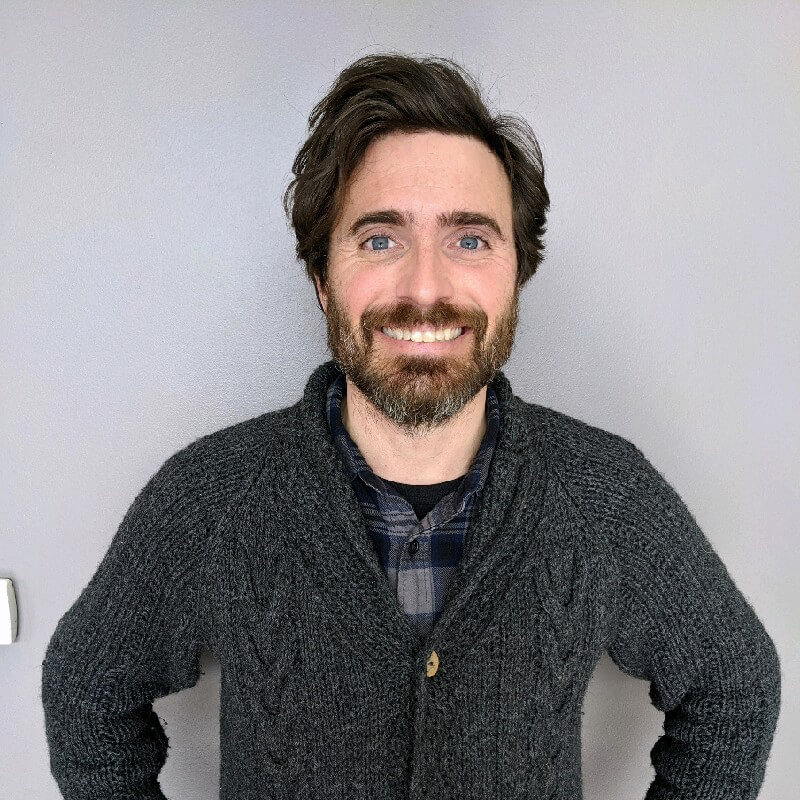
Ryan Blowers
Head of Manufacturing
ReMo Homes
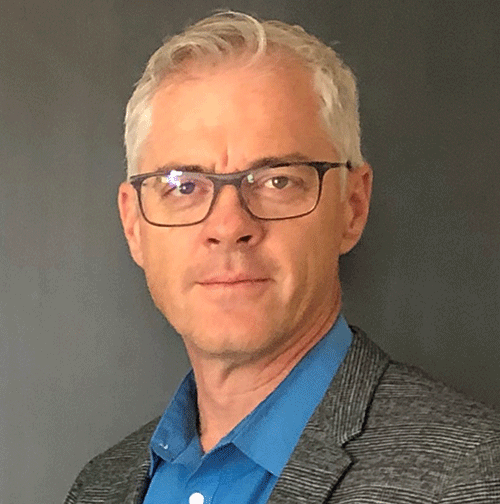
Scott Bridger
Co-Founder
ProSet LLC
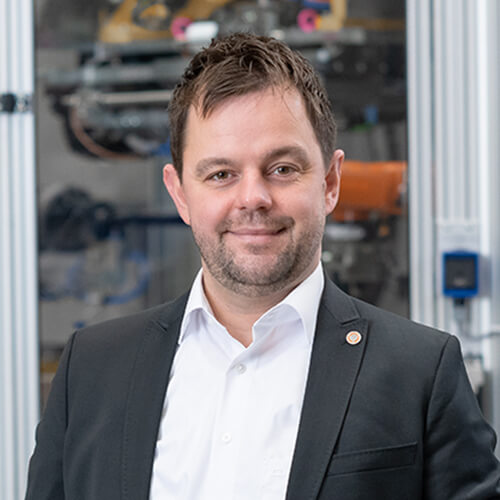
Jan-Christoph Bruhn
Head of Sales and Key Account Management
KUKA Assembly & Test GmbH
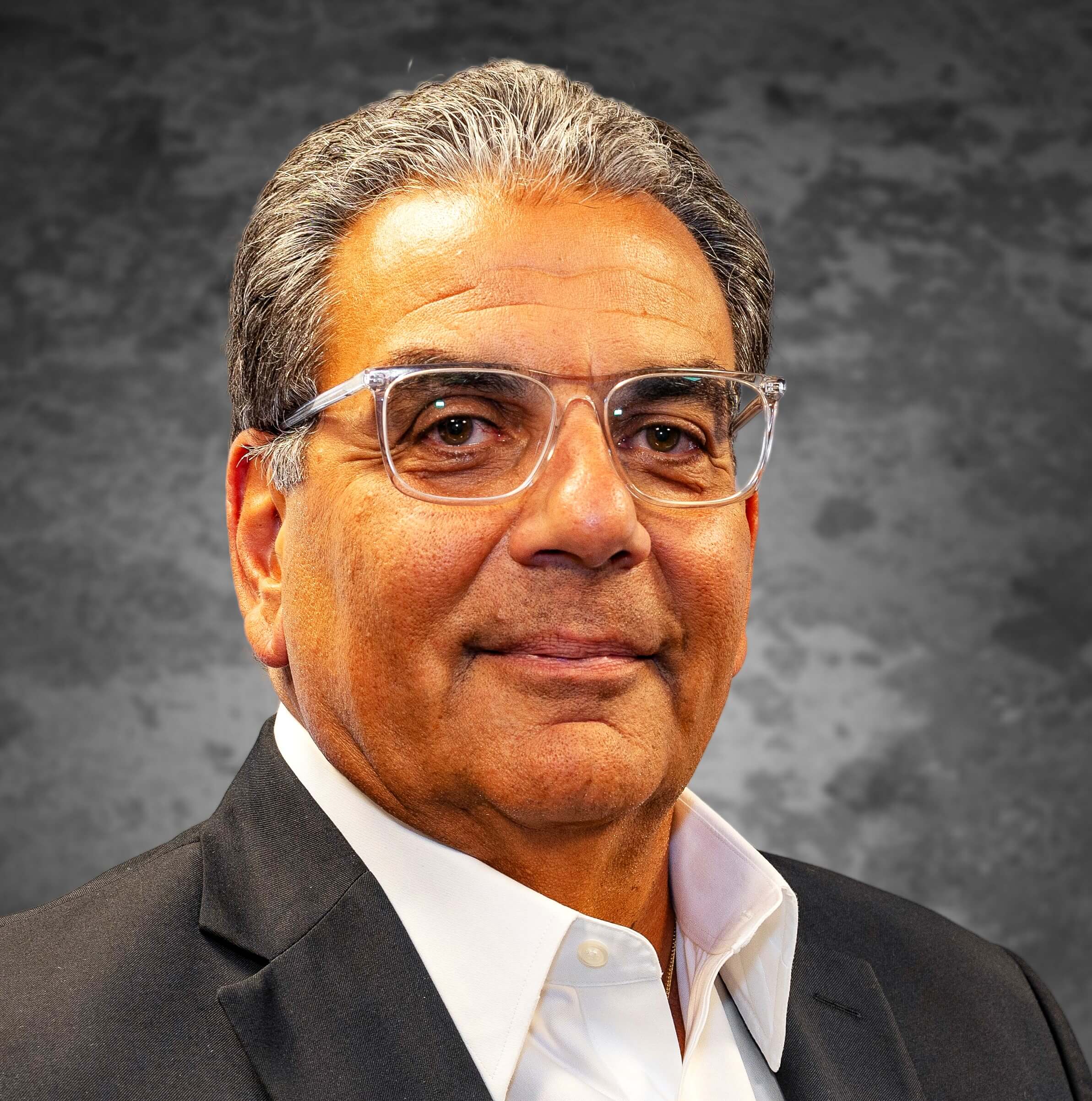
John Buongiorno
Vice President, Modular Division
Axis Construction Corp.
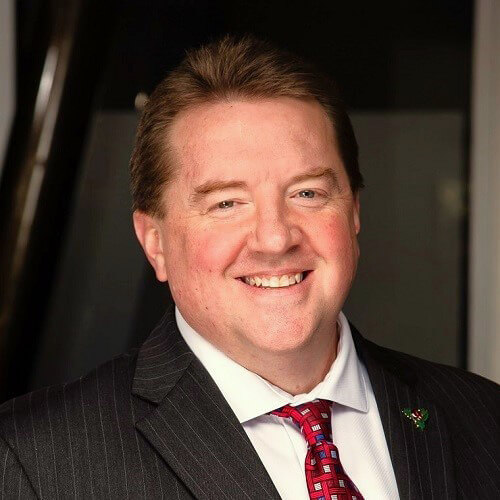
David Butler
Structural Senior Project Manager
Lochsa Engineering
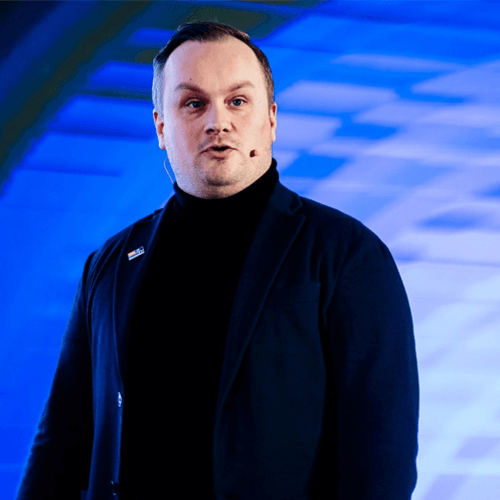
Stuart Cameron
Managing Director & MMC Lead
CES Group
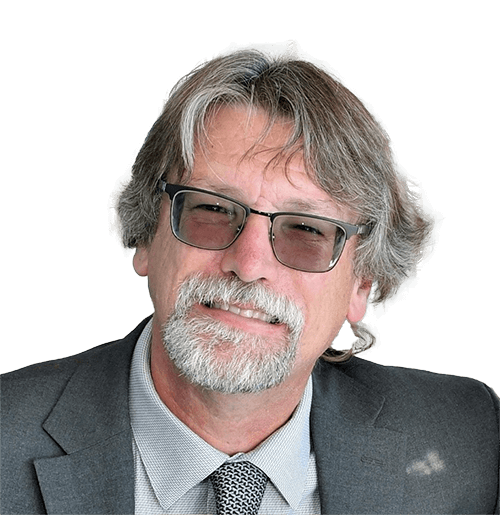
Andrew Carlson
President
Pyramid1 Inc.
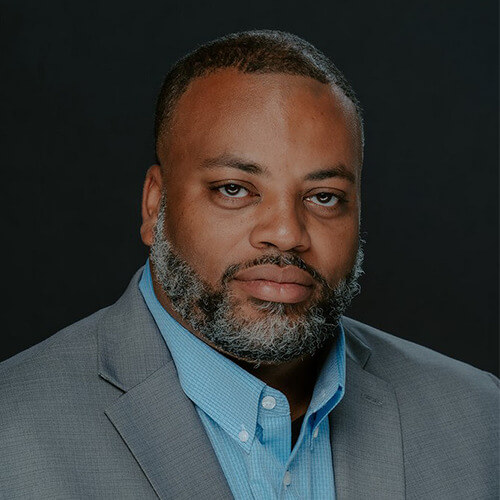
Joe Carson
Manager of Projects, Weapons Project Management Office
Los Alamos National Laboratory (LANL)
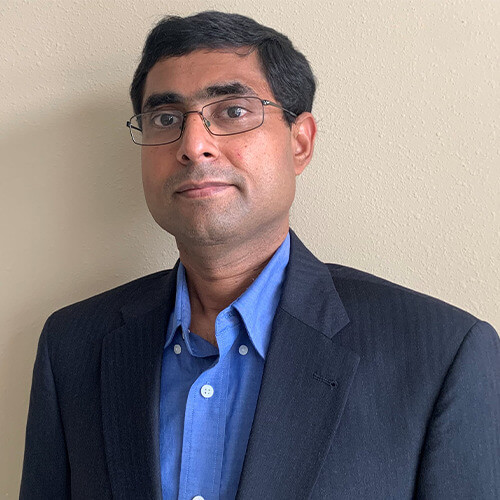
Karun Chakravarthy
Expert Business Consultant
Dassault Systèmes
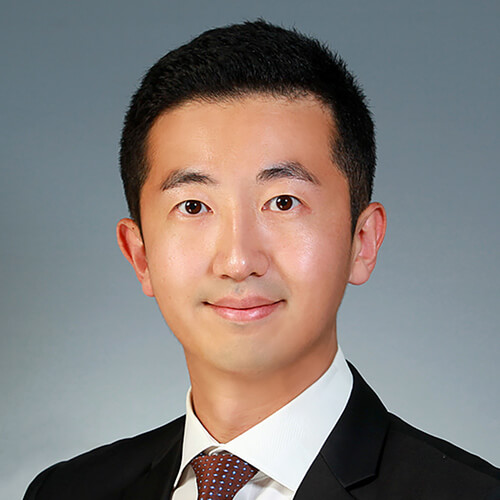
Jin Ouk Choi
Associate Professor
University of Nevada, Las Vegas
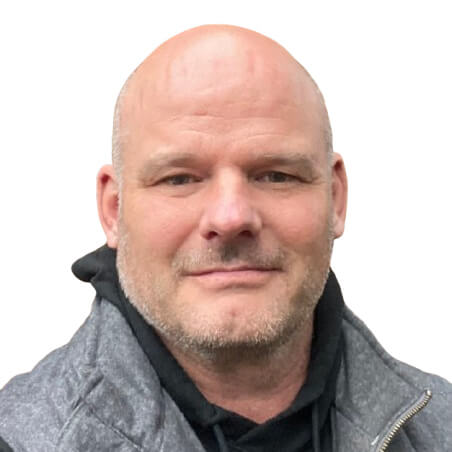
Chad Crosby
COO
Halo Halo Logistics
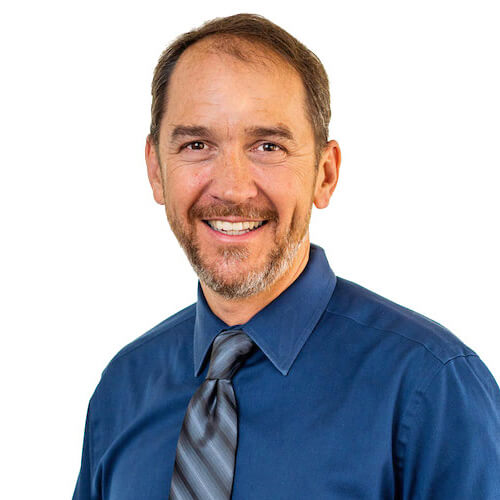
Dean Dalvit
Principal
EVstudio
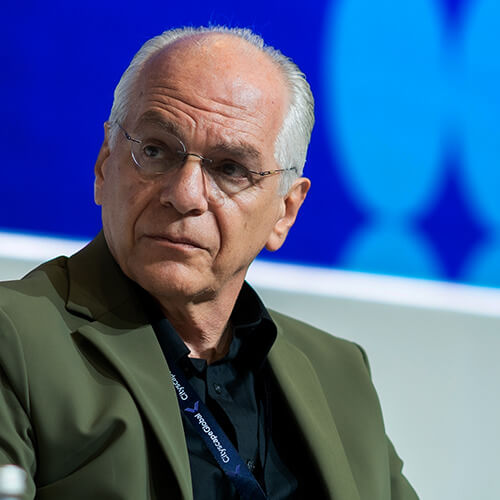
Peter DeMaria
Chief Design Officer
DeMaria Design/MID-RISE Modular
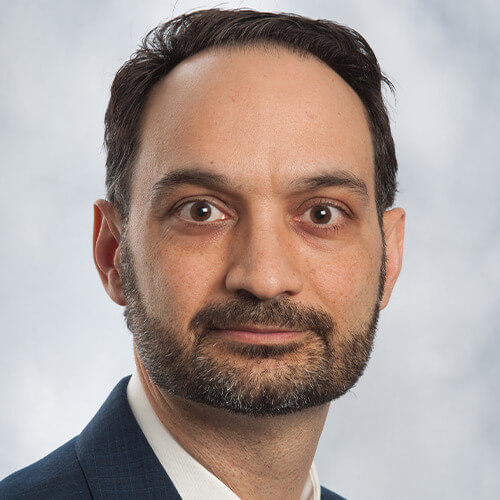
Franco DiFolco
Technical Manager, Plumbing in Construction Team
CSA Group
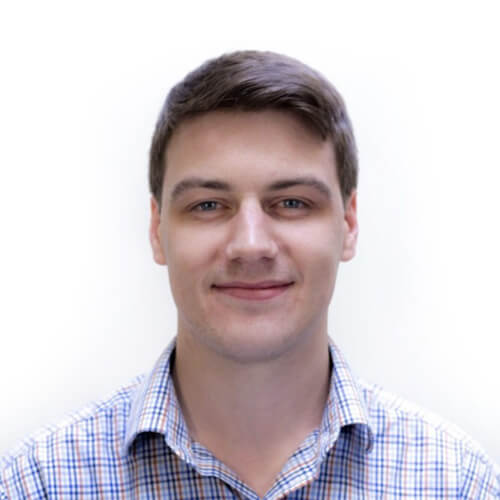
Cory Dion
Senior Design Technology Manager
Volumetric Building Companies
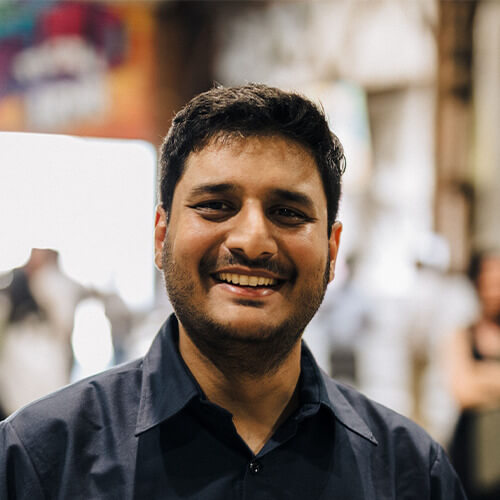
Ankur Dobriyal
Director of Offsite Innovation
ADL Ventures
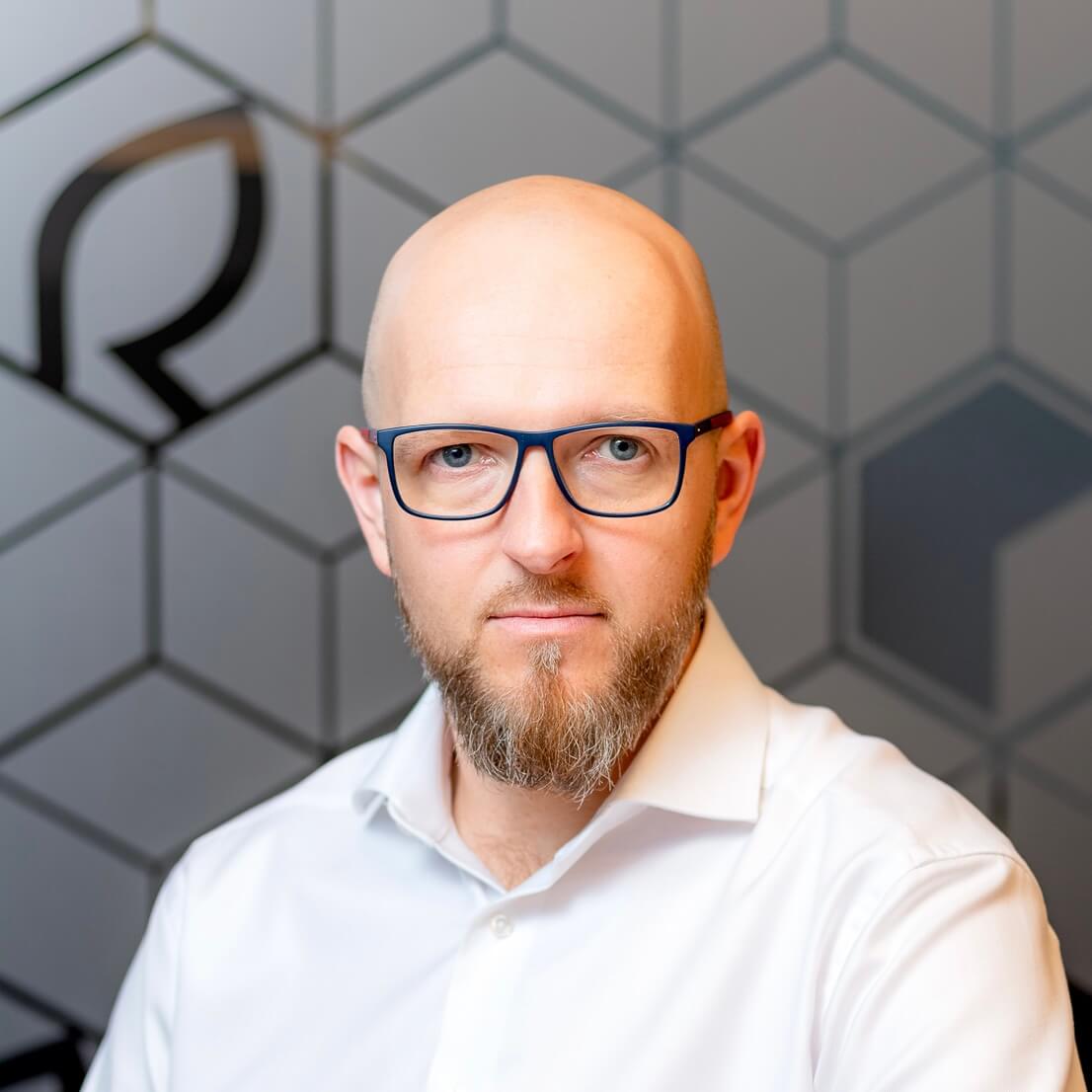
Kris Droszcz
CEO & Founder
Rebel Concept
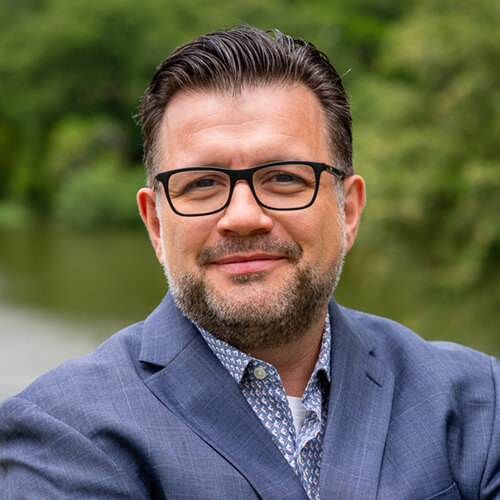
Steve Dubin
Business Development Manager
Rmax, a Sika Company
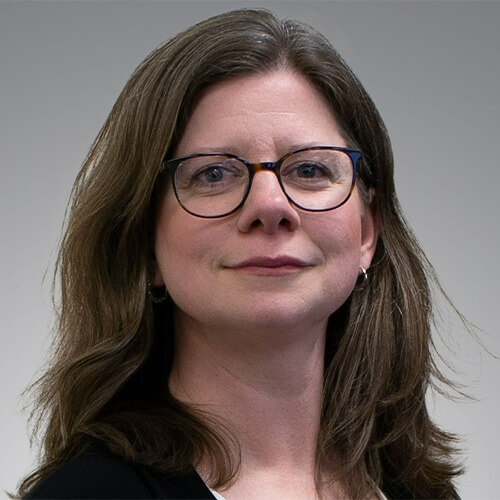
Stefanie English
Associate Vice President, Director - Engineering
Larson Design Group, Inc.
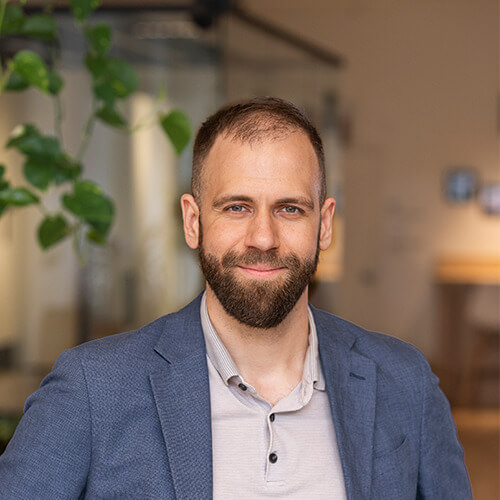
Gabriel Fournier-Filion
Co-CEO
UTILE
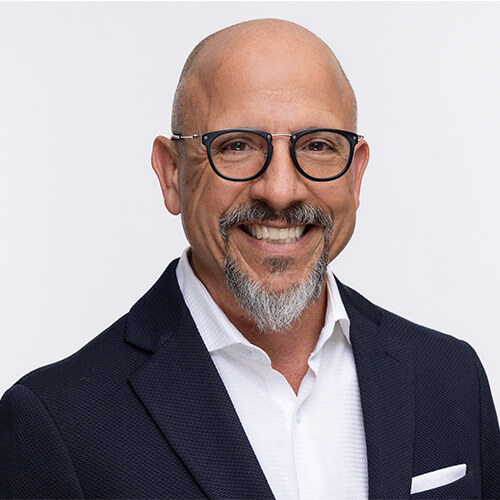
Jim Gabriel
President & CEO
MODLOGIQ & DESIGNLOGIQ
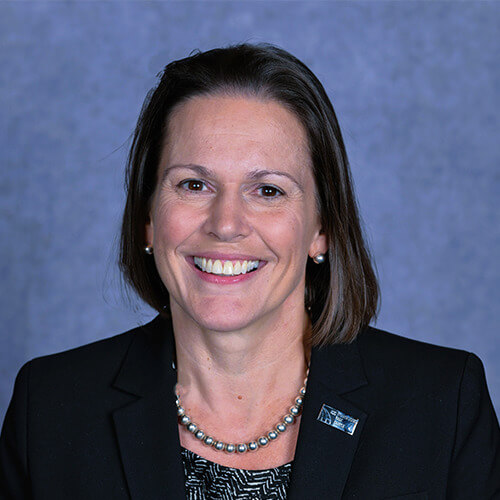
Lesley Garland
Vice President of Government Affairs
ICC
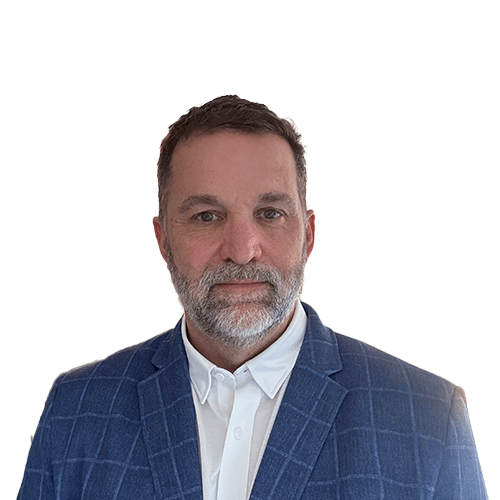
Eric Glass
UL ESH Advisory Service Manager
UL Solutions
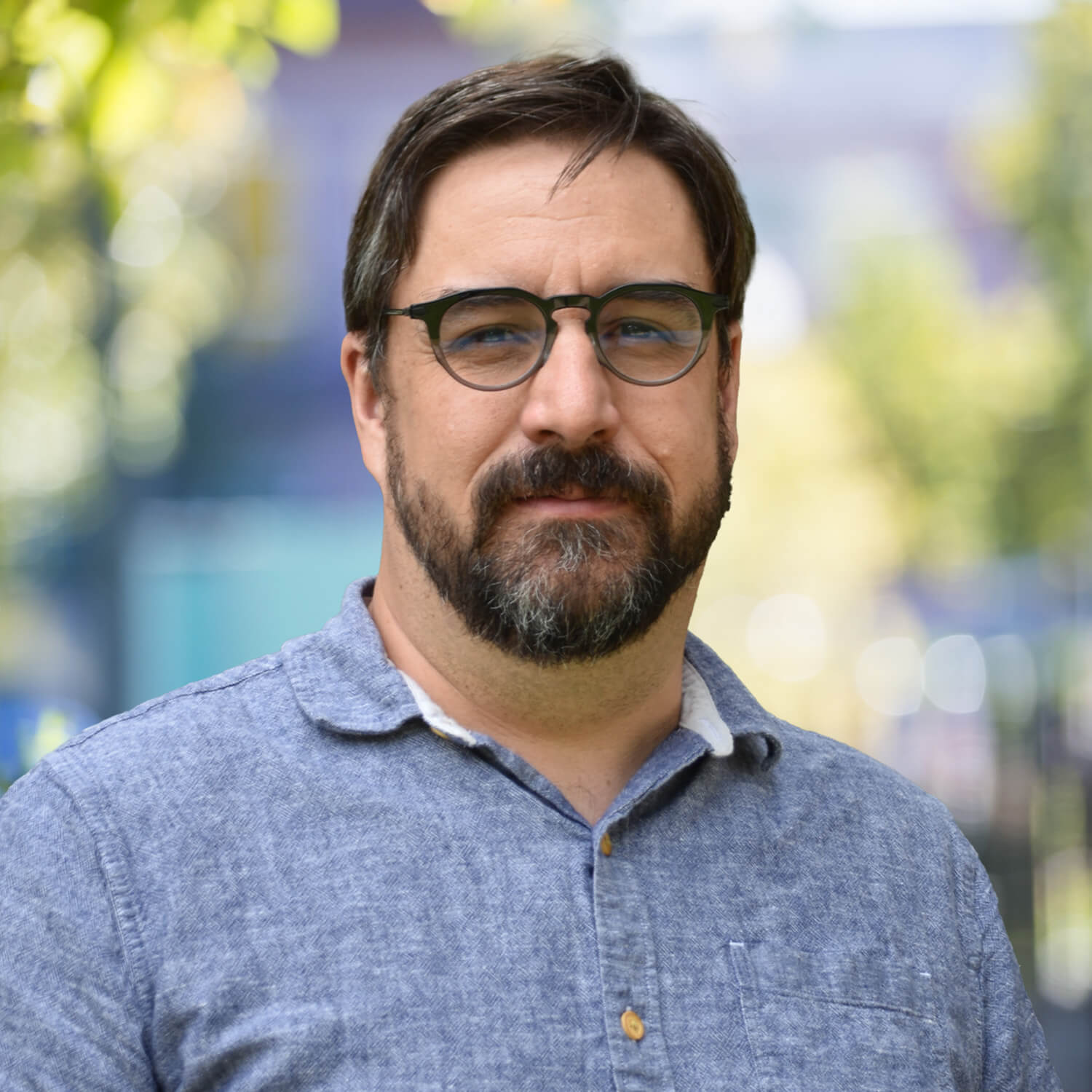
Jesse Goldman
Principal Architect
CSHQA
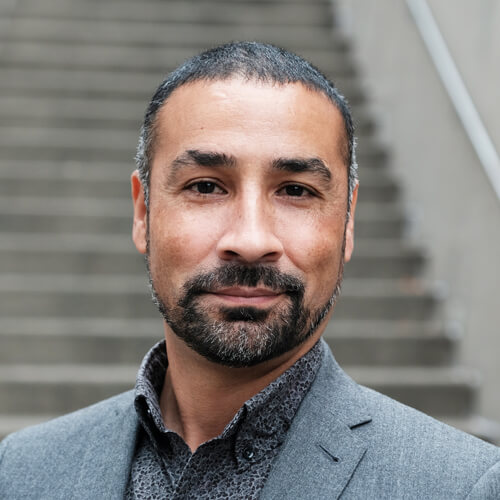
Nick Gomez
Principal - Director of Modular Design & Construction
AO / Architects Orange
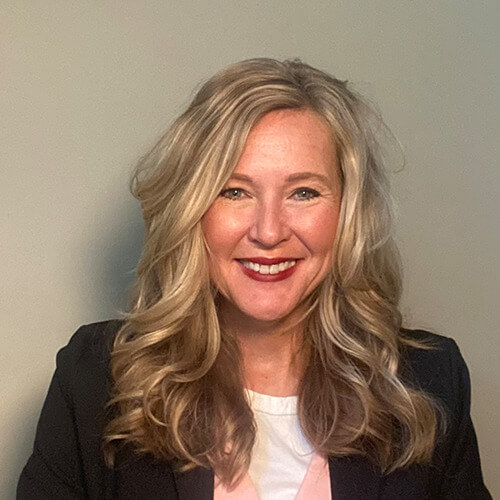
Audree Grubesic
Chief Revenue Officer
Merlin AI
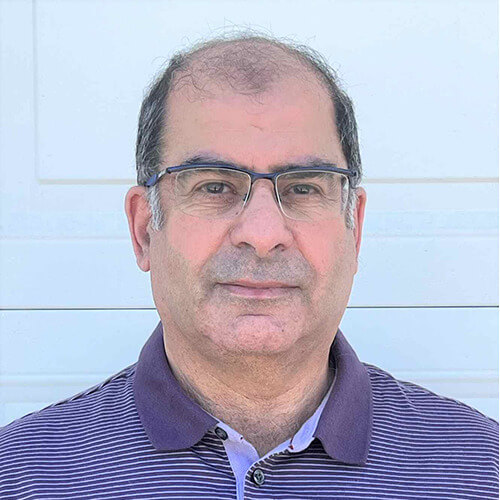
Khaled Habib
Principal Technical Lead, Structural & Construction
CSA Group
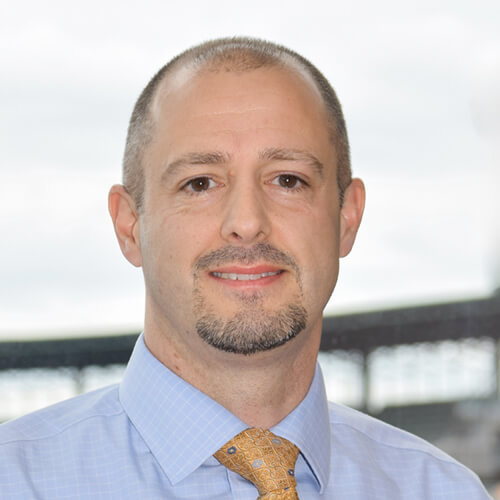
Jason Hannah
Vice President
Whiting-Turner Contracting Company
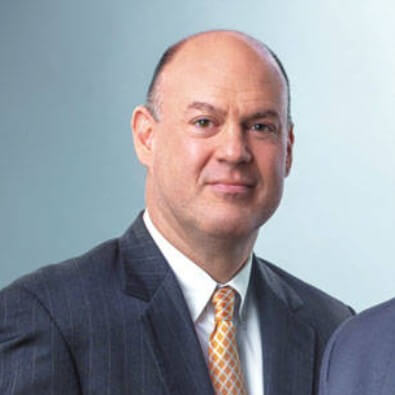
Tom Hardiman
Executive Director
Modular Building Institute
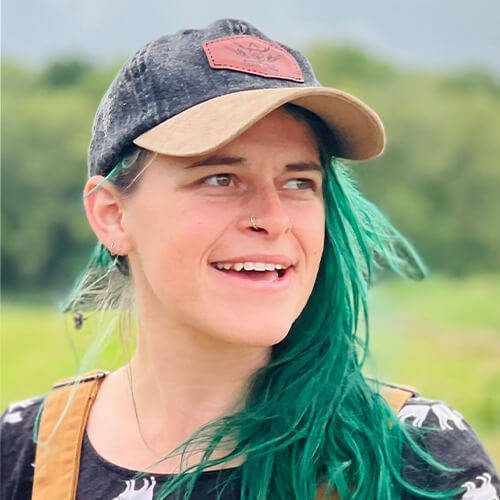
Michaela Harms
VP of Mass Timber
Sterling Structural
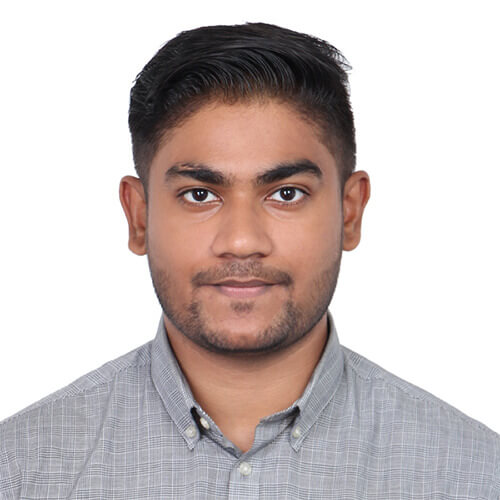
Sibgat Hasan
Former Graduate Research Assistant
University of Nevada, Las Vegas
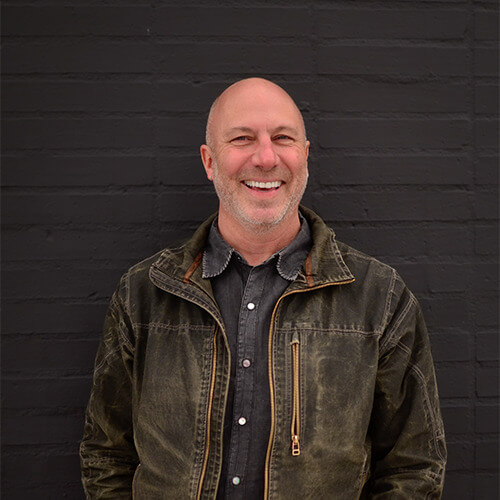
Christopher Herr
Design Director
Adam Berger Development, LLC
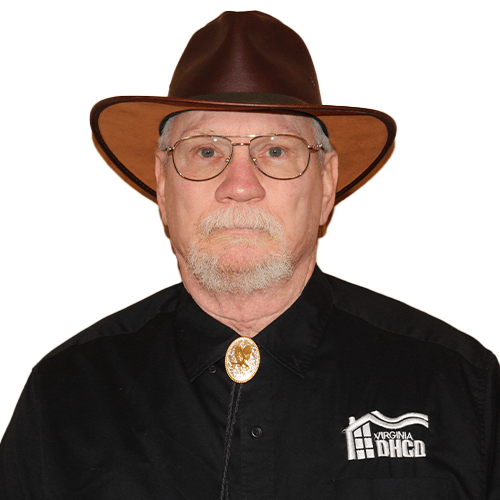
Brian Hilderbrand
Construction Regulation Administrator
Virginia
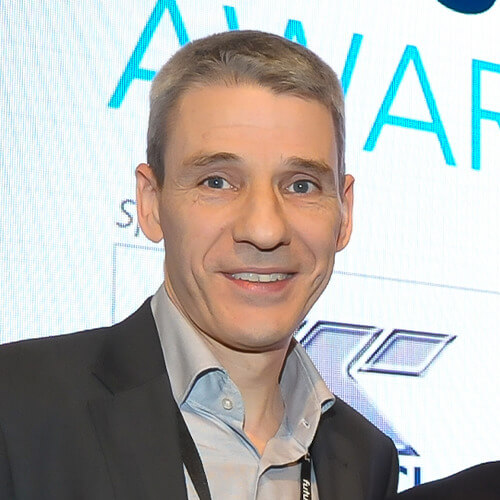
Michael Hough
Director
MJH Structural Engineers
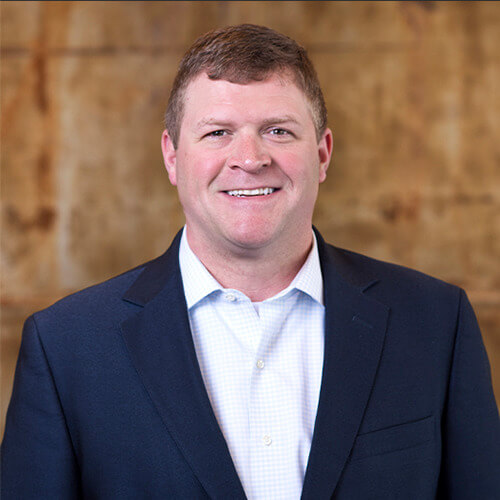
Jim House
Senior Consultant
FMI Consulting
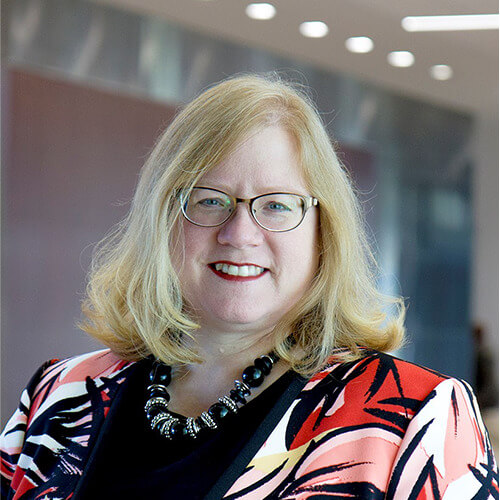
Tammy Huddleston
VP Design, Code, & Construction
Dallas Fort Worth International Airport
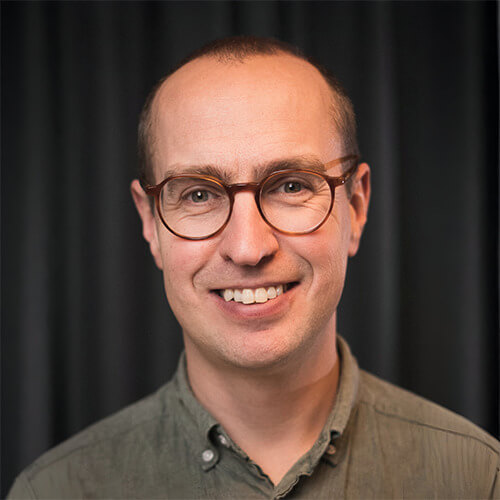
Per-Olof Hulthe
CEO
Poji AB
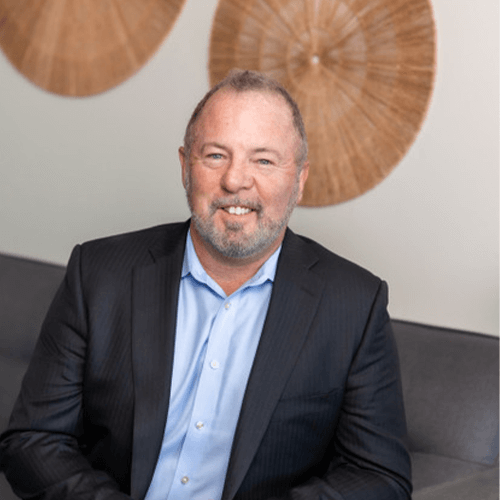
HR Huntsman
President/Founder
Leader's Edge
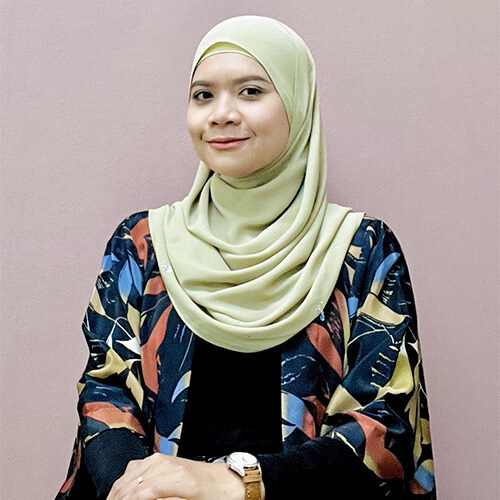
Ts. Rozainah (Dina) Ibrahim
Head of Business Development
Construction Industry Development Board (CIDB)
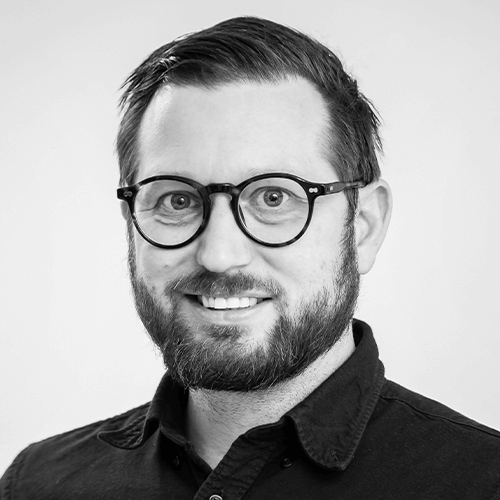
Patrik Jensen
CEO
Moko AB
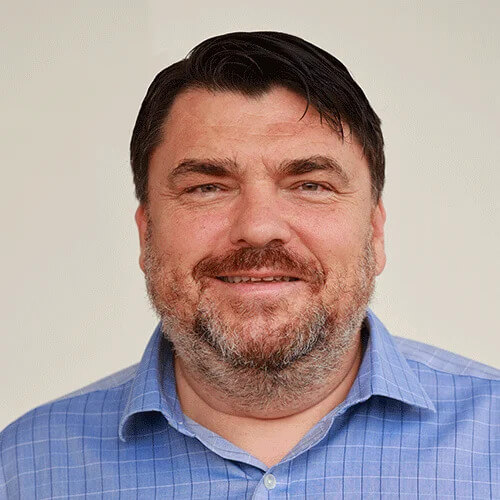
Bostjan Jevsek
International Business Development Director
Piva Group S.P.A
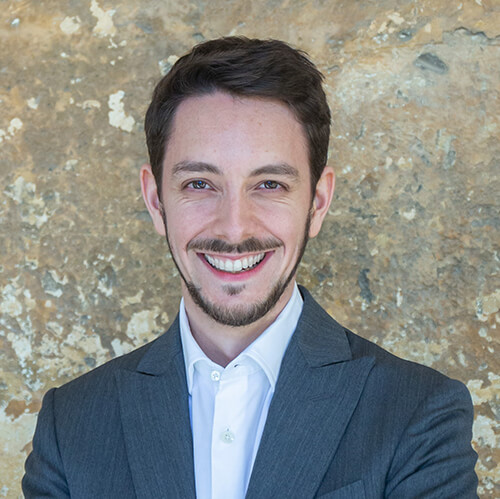
Edward Jezeph
Senior Manager & MMC Lead
Homes England
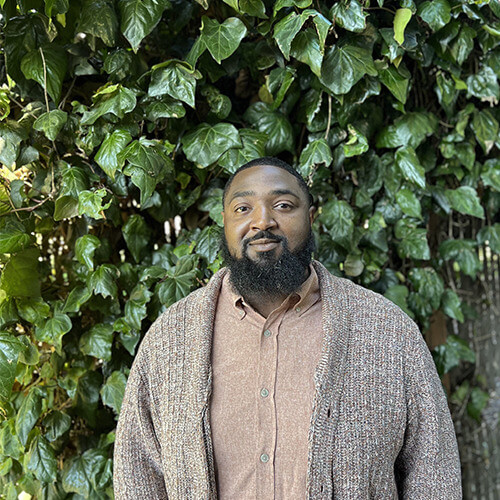
Dijon Jones
Senior Systems Manager
Volumetric Building Companies
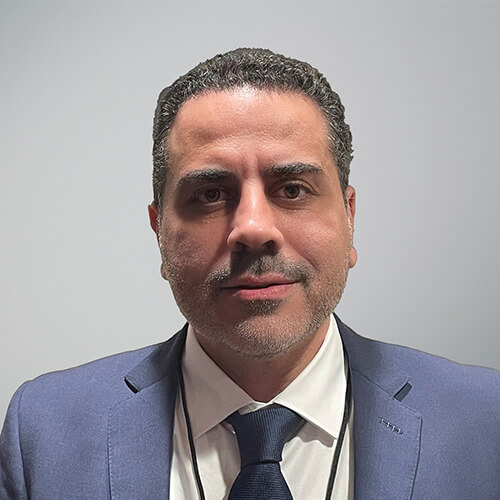
Ghassan Joudi
Program Director
HNTB Corporation
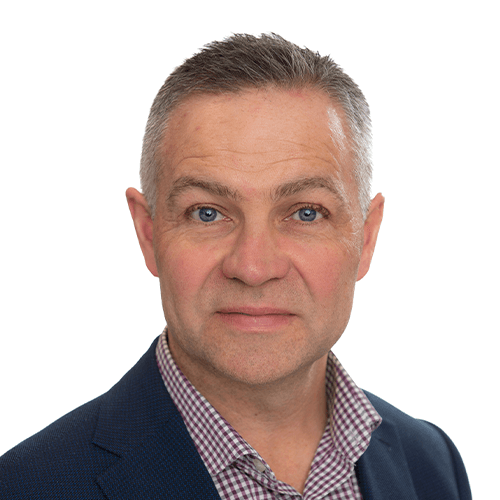
Rhys Kane
Director of Business Development
ROC Modular Inc.
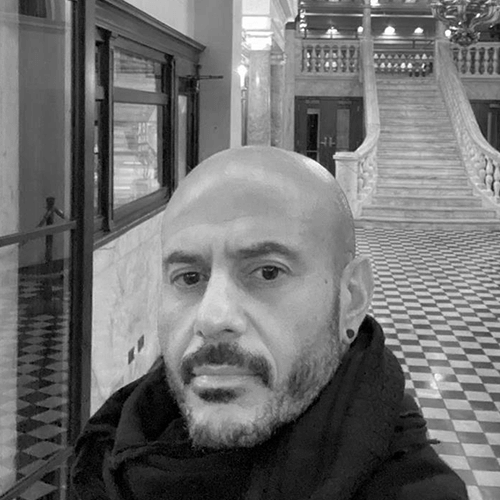
Fouad Khalil
Principal
Modly LLC
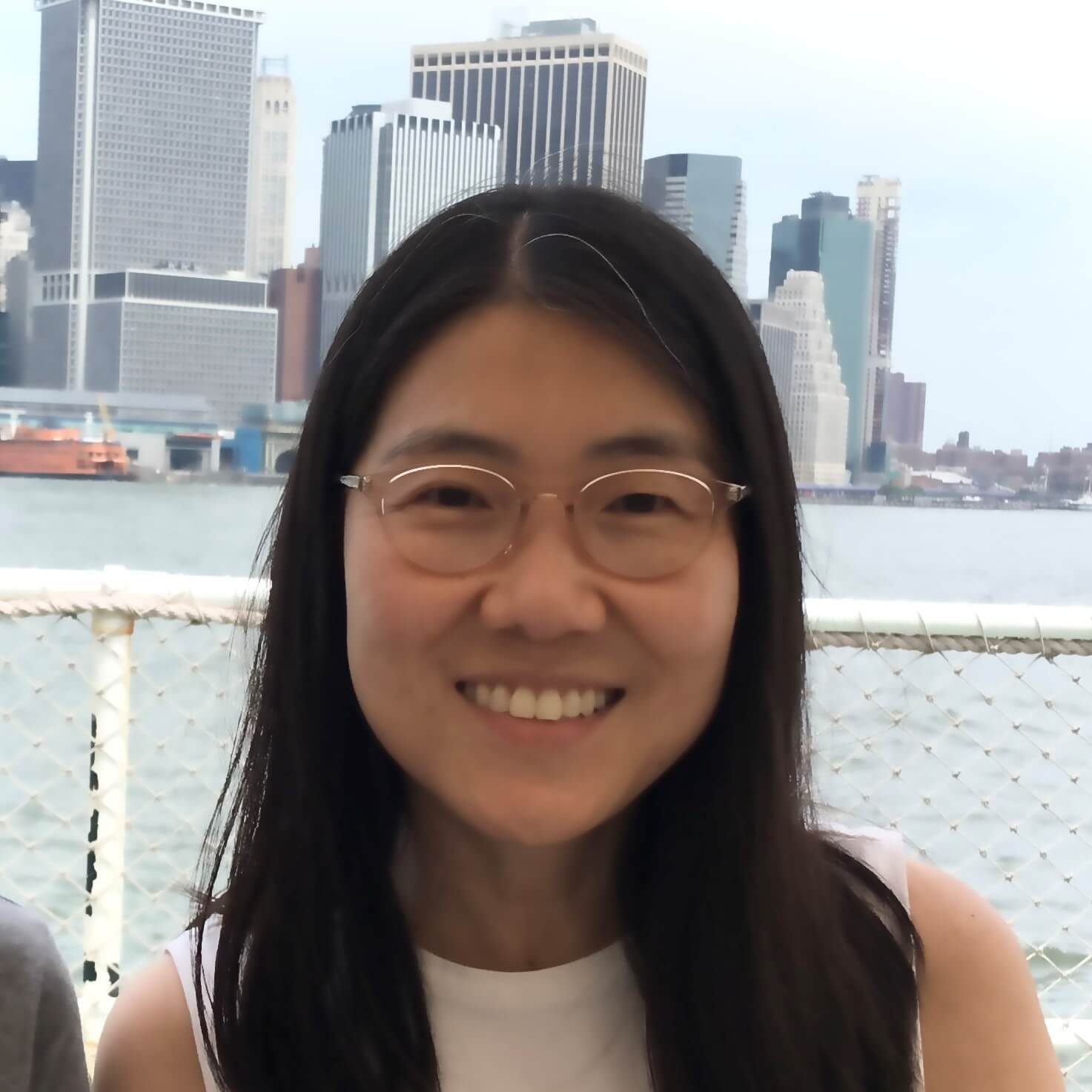
Karen Kim
Senior Design Associate- East Coast
Volumetric Building Companies
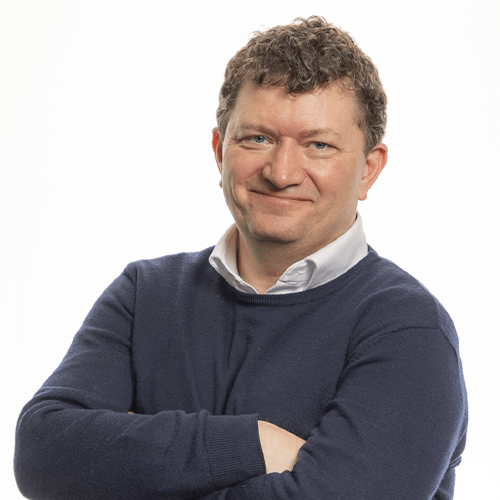
Pat Kirwan
Associate Director, Head of Industrialised Design and Construction
Reddy Architecture + Urbanism
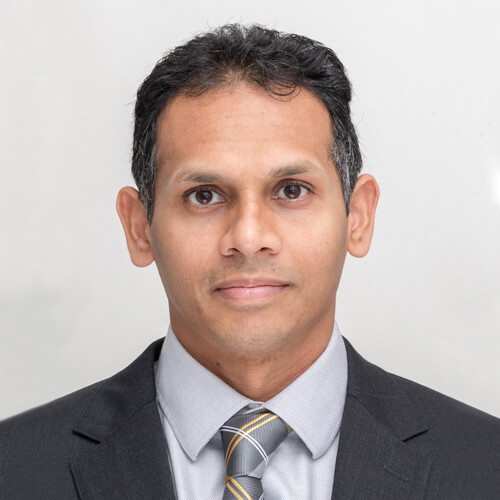
Vamsi Kumar Kotla
CEO
ReMo Homes
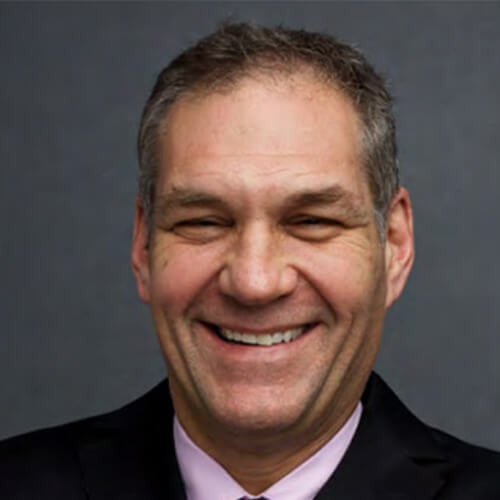
Roger Krulak
President & Founder
FullStack Modular
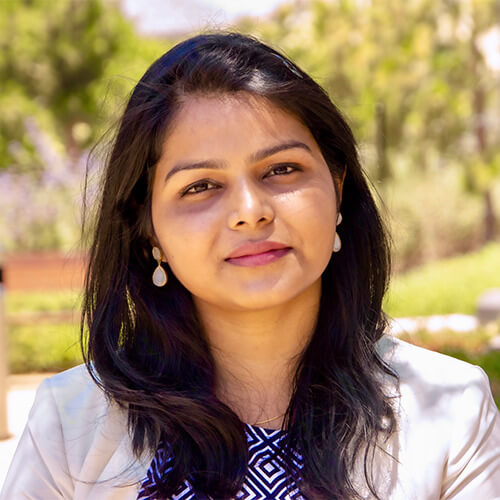
Sneha Kumari
Co-Founder/CEO
Merlin AI
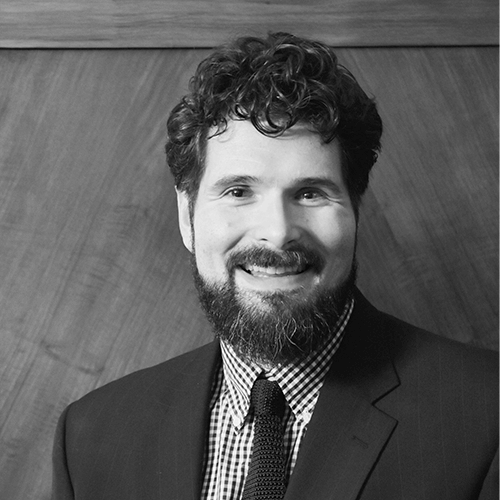
Greg Kuta
President & CEO
Westline Capital Strategies Inc.

Andy Kwong
Product Manager, Standards Education and Services
CSA Group
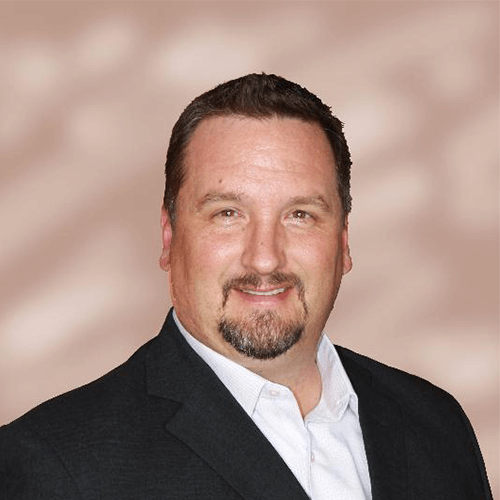
Matt Laase
Principal Architect
Jackson | Main Architecture
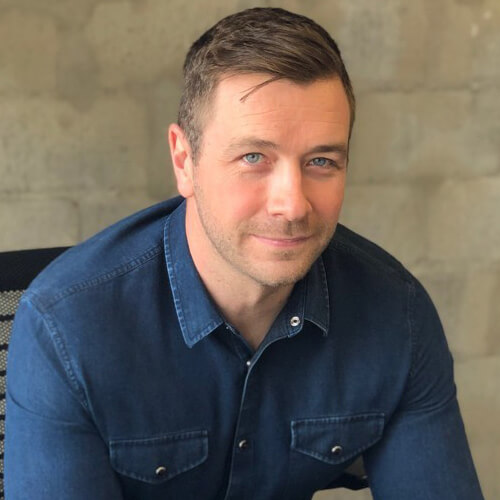
Cooper Lane
Vice President, Sales
Reko Automation Group Inc.
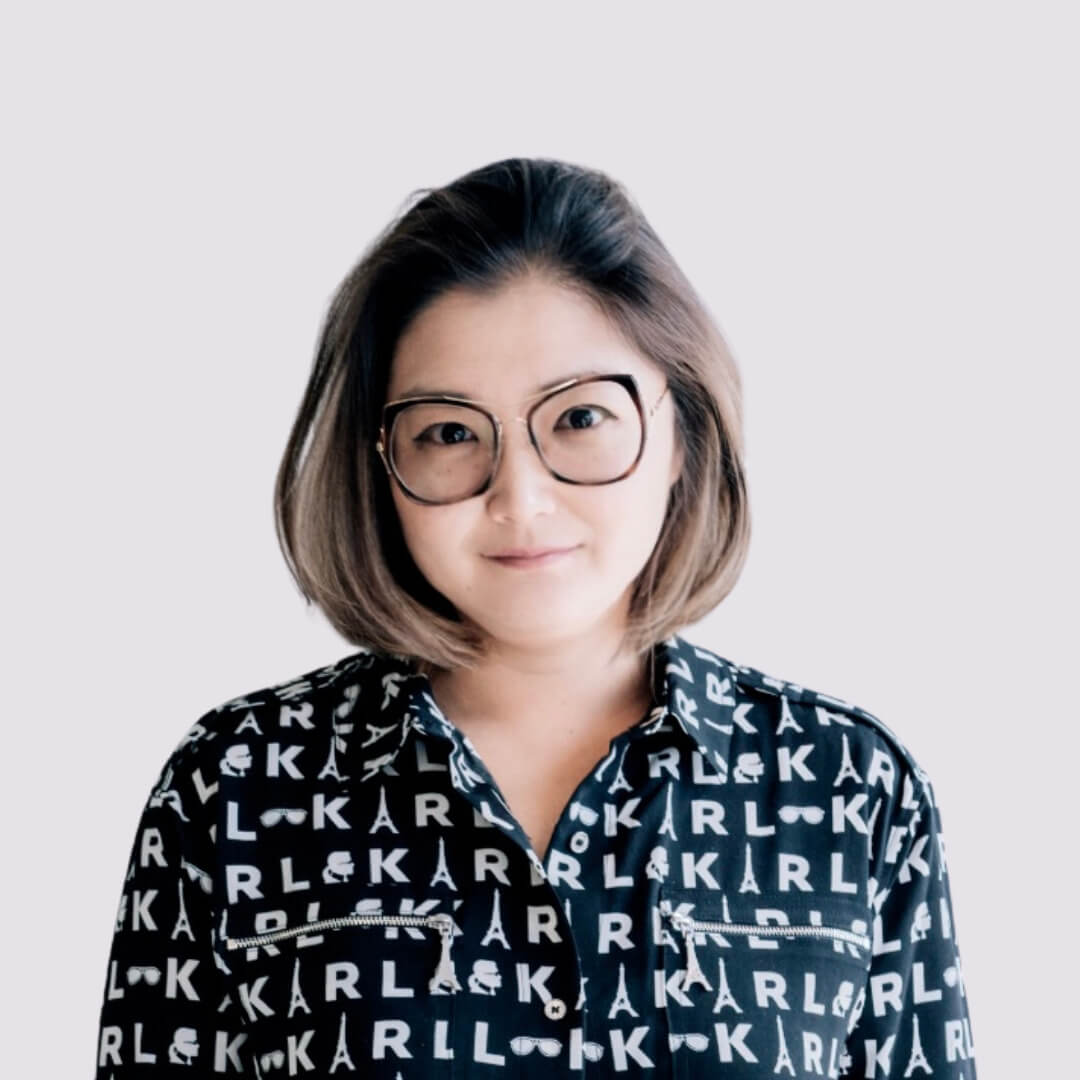
Eisa Lee
Partner Architect
xL Architecture & Modular Design
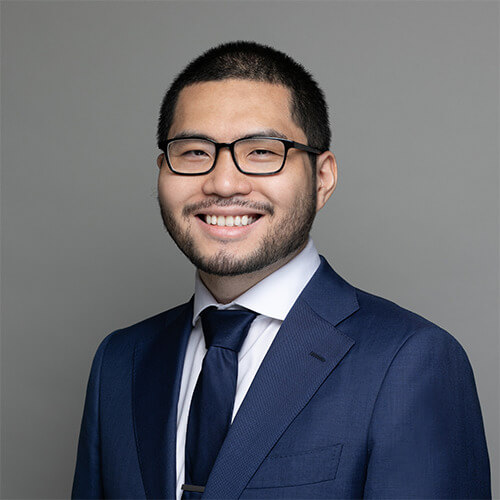
Jimmy Liang, PE
Senior Engineer
Murray Engineering
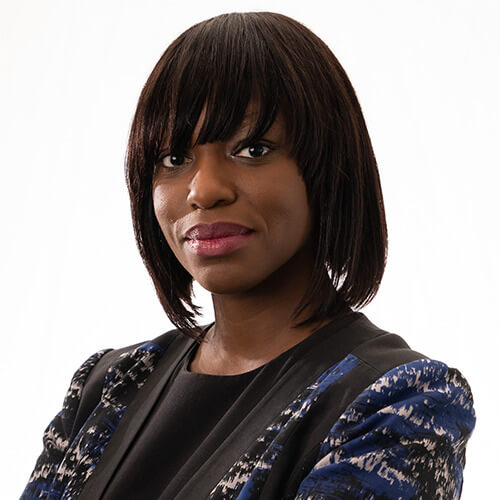
Sara Logan
Head of Design, Principal Architect
Volumetric Building Companies
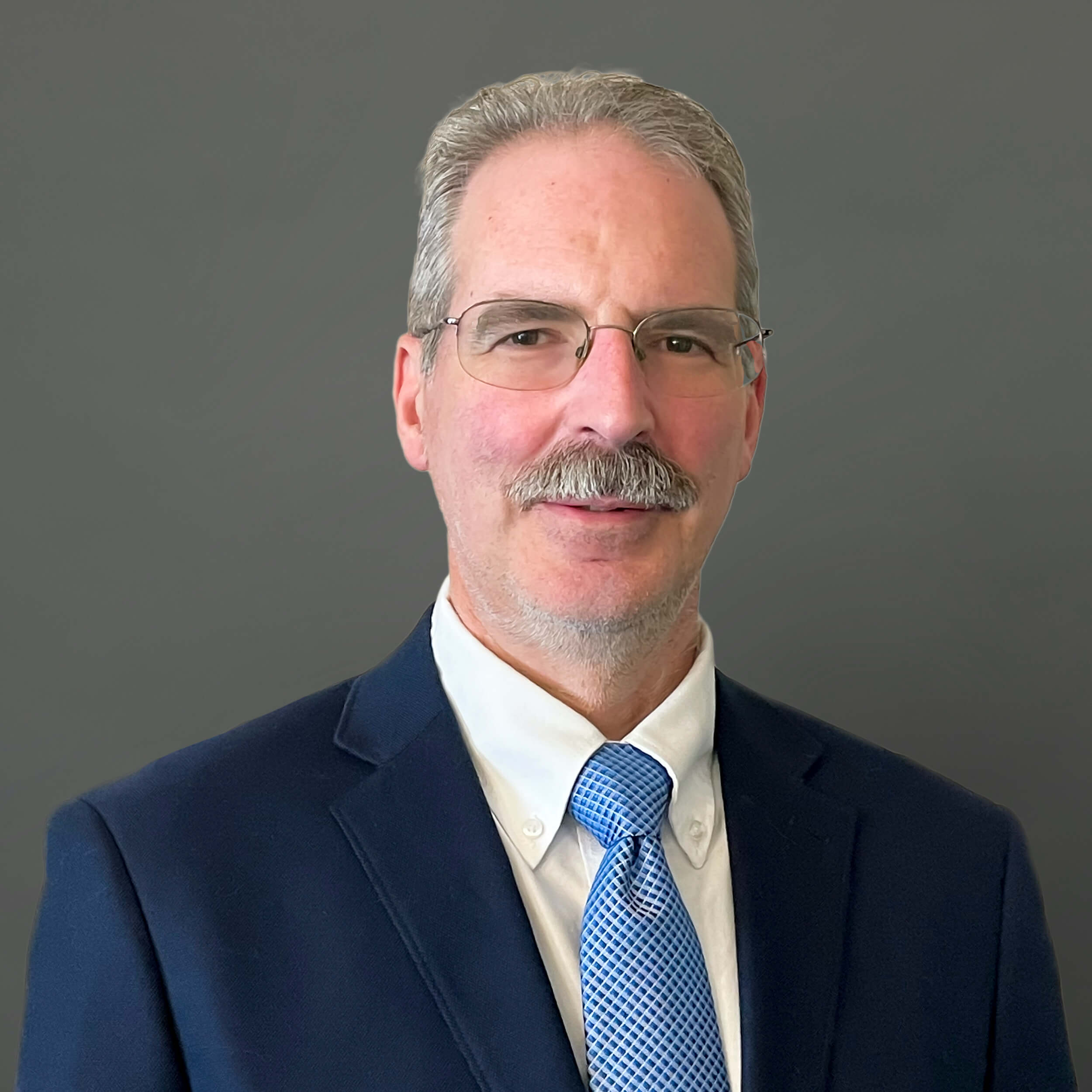
Michael Lynch, PE, SE
Associate/VP Modular
Murray Engineering
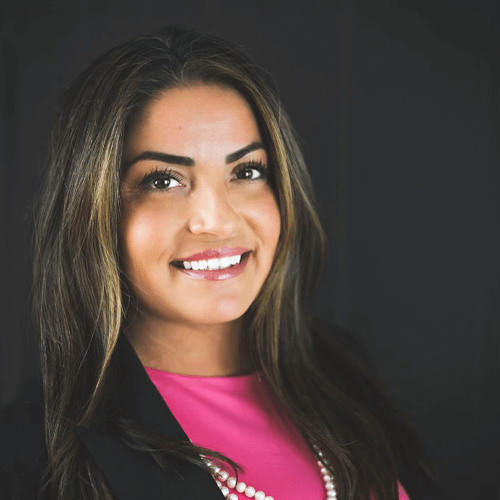
Merrick Macomber
Founder/CEO
Modular Maven
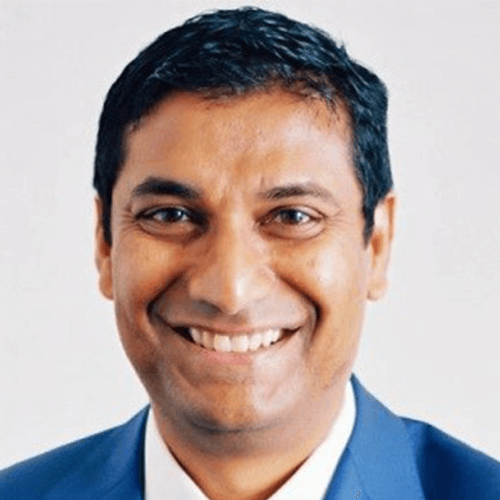
RJ Mahadev
Co-Founder/CEO
RaaP Builders
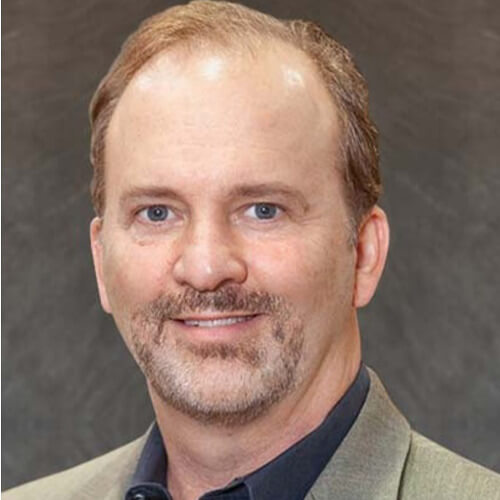
Ron Mann
Vice President
Compu Dynamics Modular
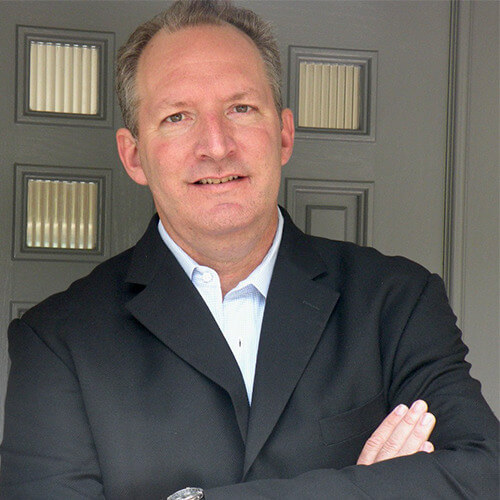
Michael Mathews
CEO/Founder
ASSEMBLAGEworks

Ryan McIntosh
Director of Design & Engineering
Silver Creek Modular
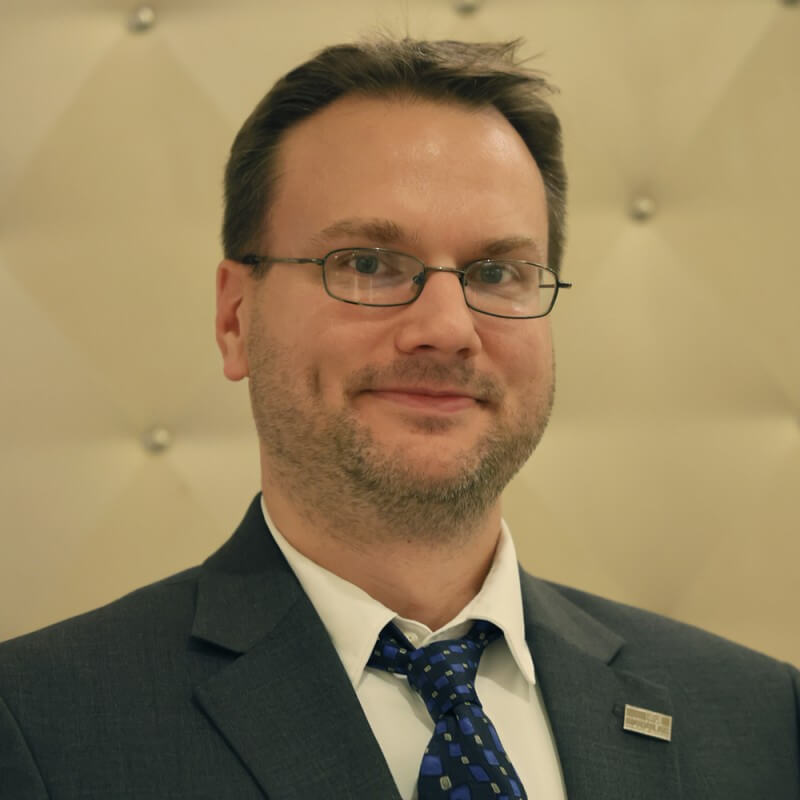
John McMullen
Marketing Director
Modular Building Institute
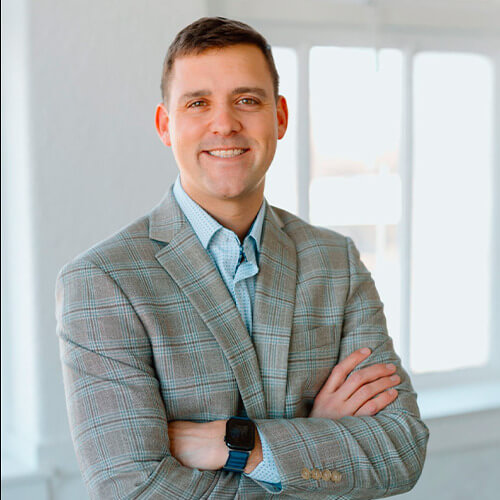
Alex Mead
Risk Management Consultant
StoneX Financial Inc.
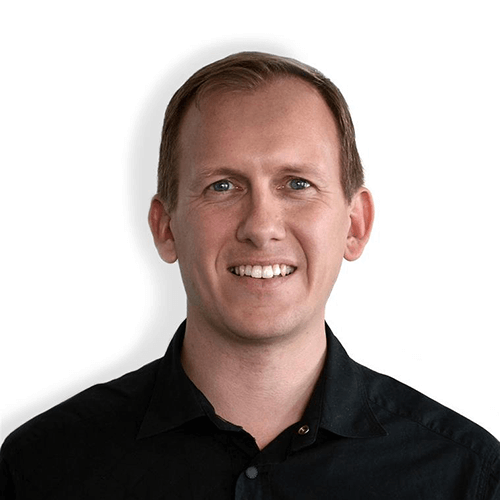
Nuri Miller
AEC Industry Solution Technical Senior Manager
Dassault Systèmes
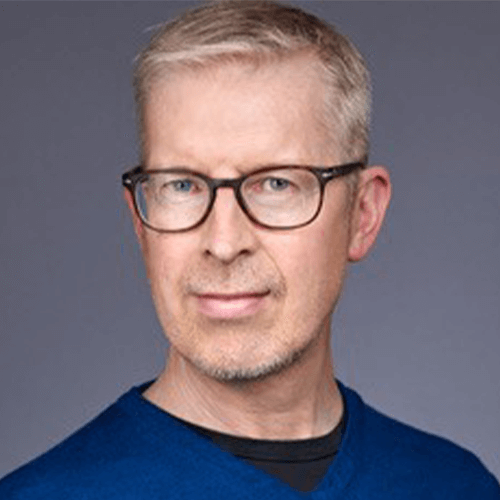
Alan Milne
European Membership Director
Modular Building Institute
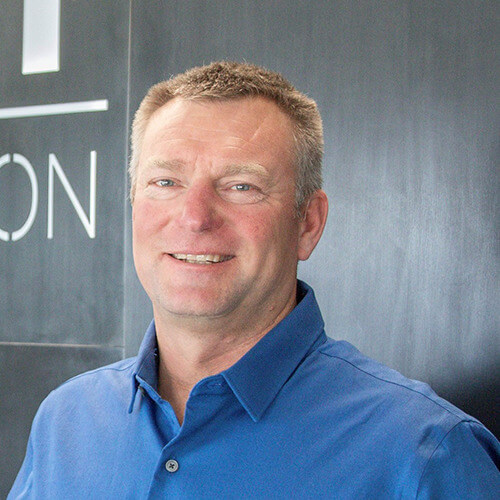
Matt Mitchell
Co-Founder
ProSet LLC
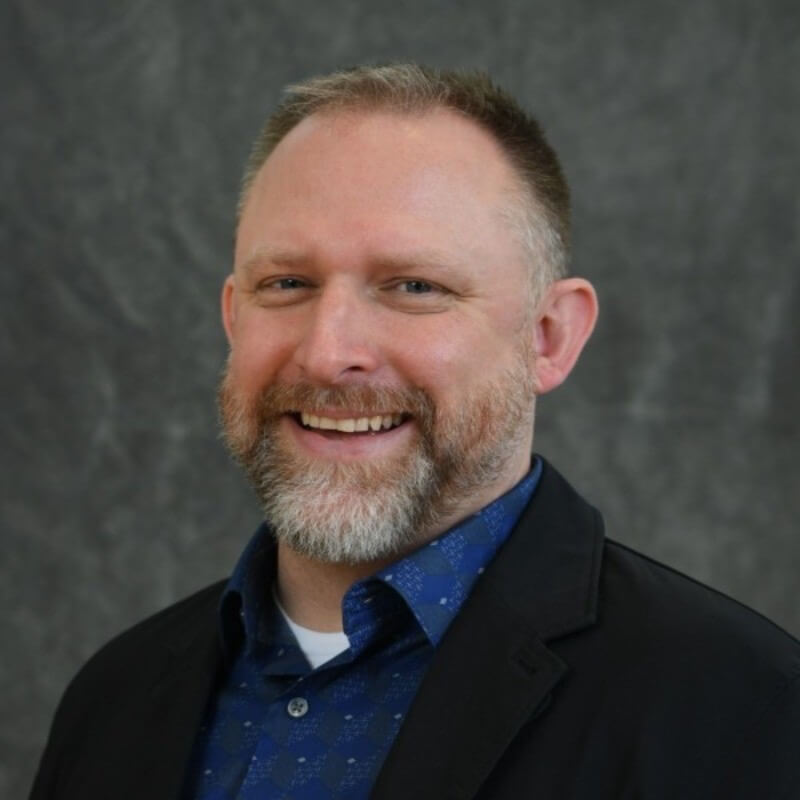
CJ Myrick
Chief Construction Officer
ModCM
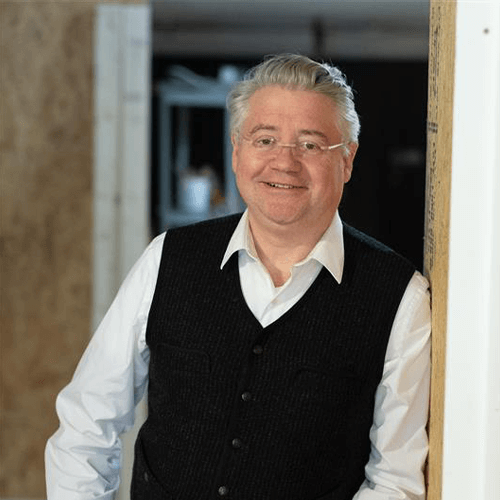
Jason Van Nest
Executive Director, Center for Offsite Construction
New York Institute of Technology
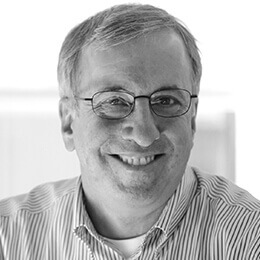
Peter Noone
Managing Principal
Solomon Cordwell Buenz
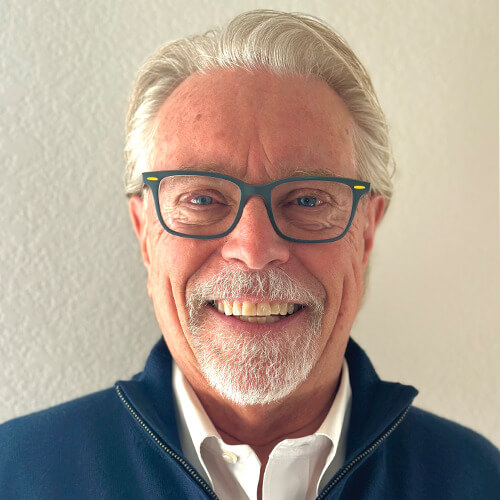
Otis Odell
Housing Sector Lead
HED Design
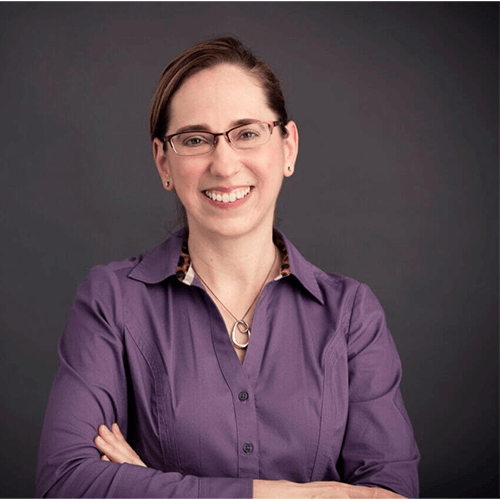
Heather Packard
Professional & Workforce Development Director
Modular Building Institute
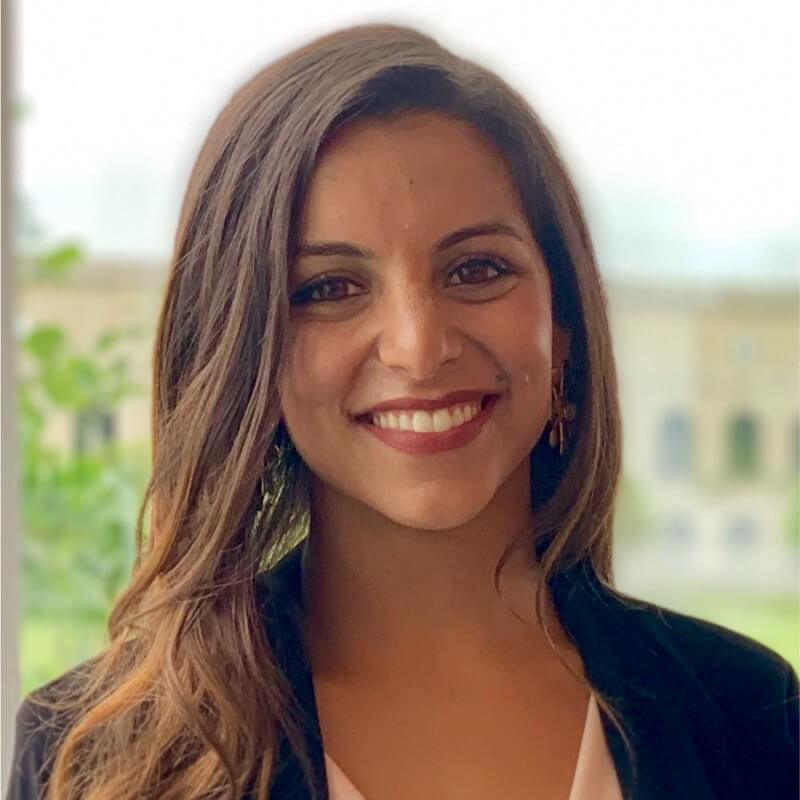
Apoorva Pasricha
Chief Operating Officer
Cloud Apartments
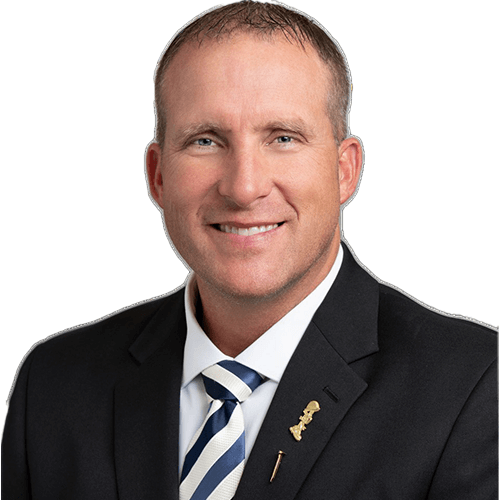
Tom Peterson
Utah Building Official
Utah House of Representatives
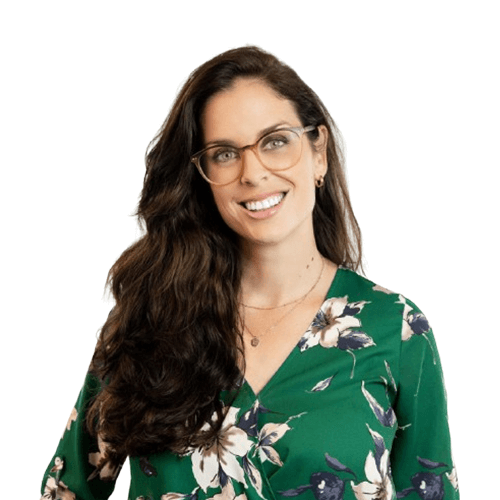
Beth PopNikolov
CEO
Venveo
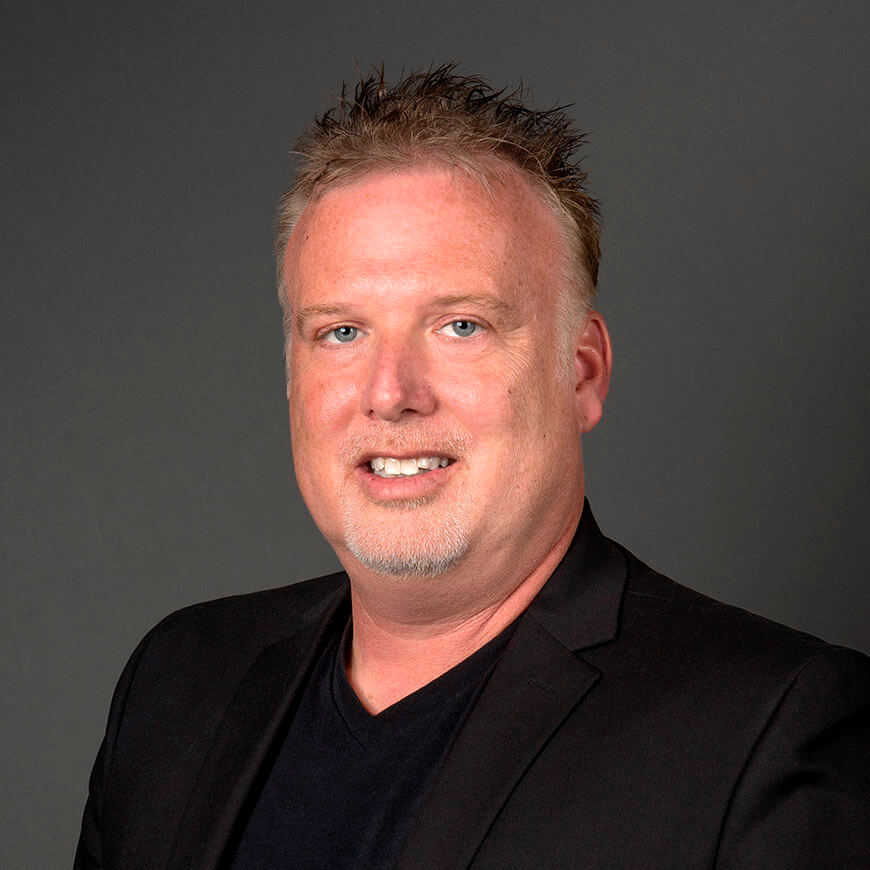
Matthew Porreca
Principal & Design Director
LPA Design Studios
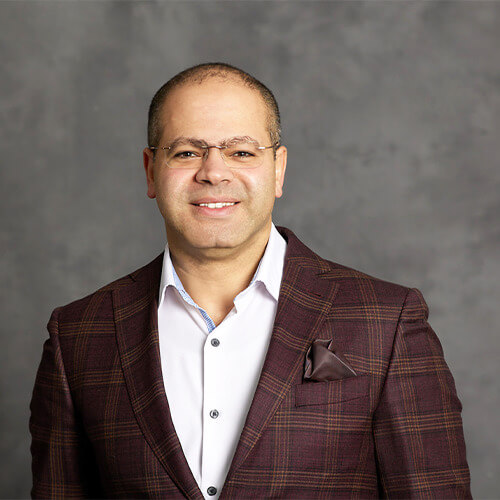
Amr Raafat
Chief Innovation Officer
Windover Construction
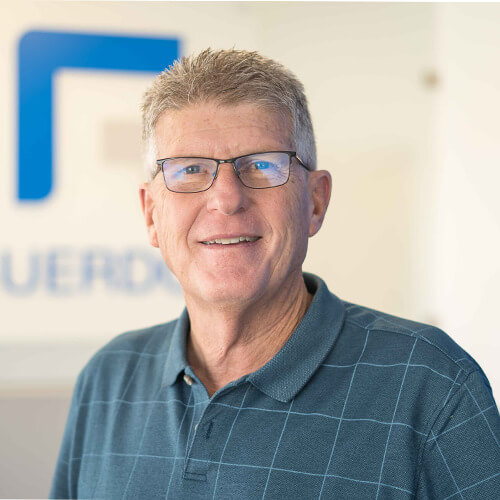
Tommy Rakes
CEO
Guerdon, LLC
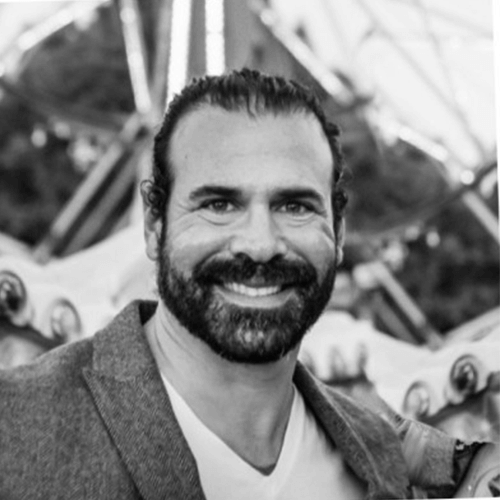
Matthew Rapa
Vice President of Construction
Cloud Apartments
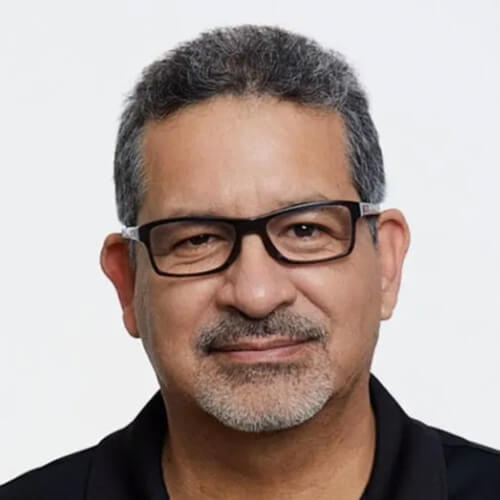
Diego Rivera
Chief Executive Officer
Framesteel/MID-RISE Modular

Rory Rubin
Founder/CEO
SI Container Builds
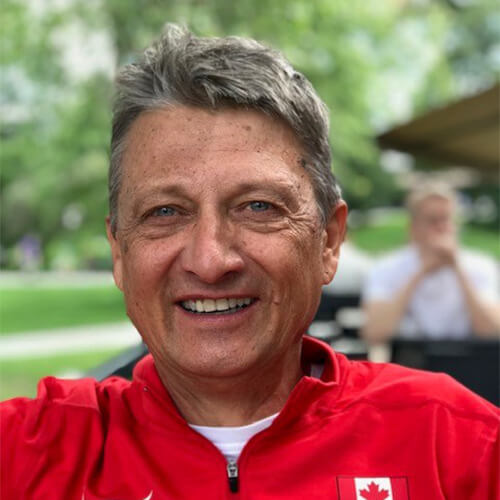
Jerry Rynda
Director, Business Development and Marketing
Buttcon Holdings
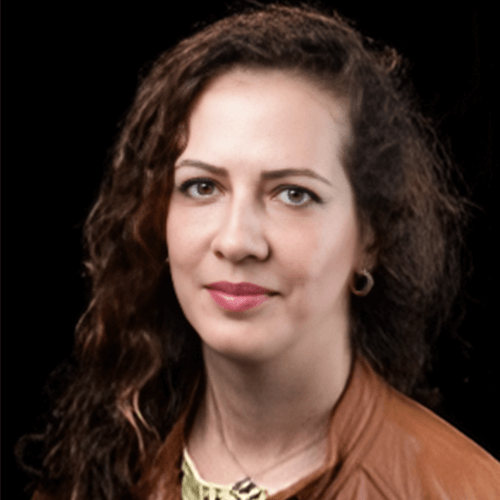
Arezou Sadoughi
Assistant Professor
Appalachian State University & Founder, MassTiMod
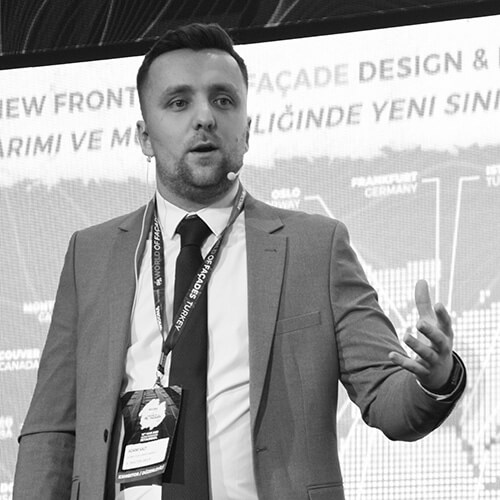
Adam Salt
Head of Global Sales Modular Offsite
A Proctor Group
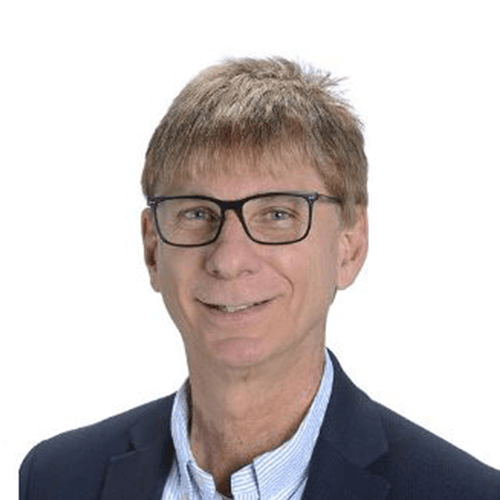
Eric Schaefer
Chief Business Development Officer
Fading West
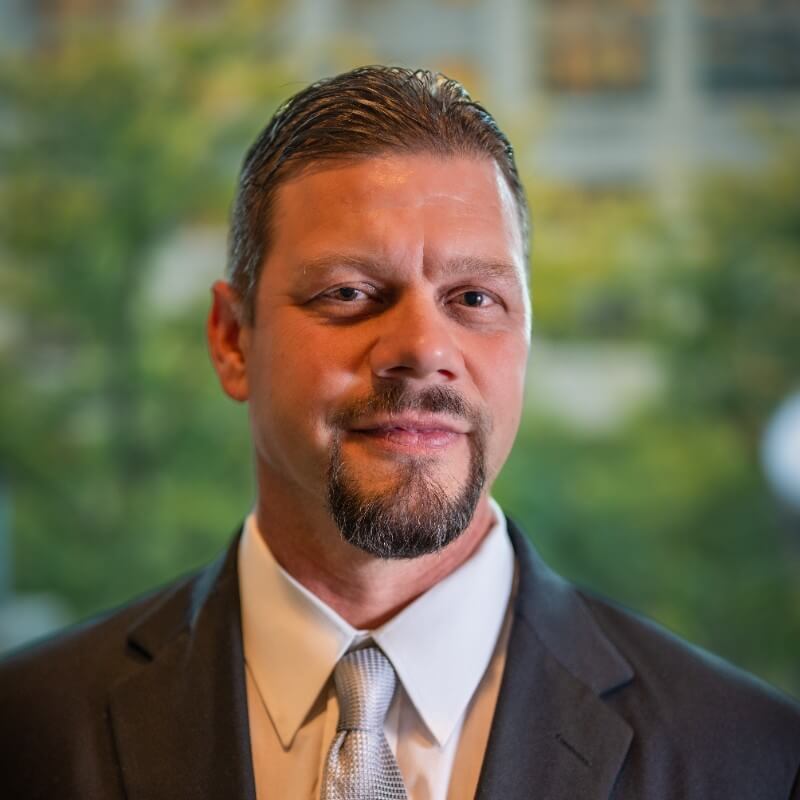
Dave Sikora
Business Development Director
Modular Building Institute
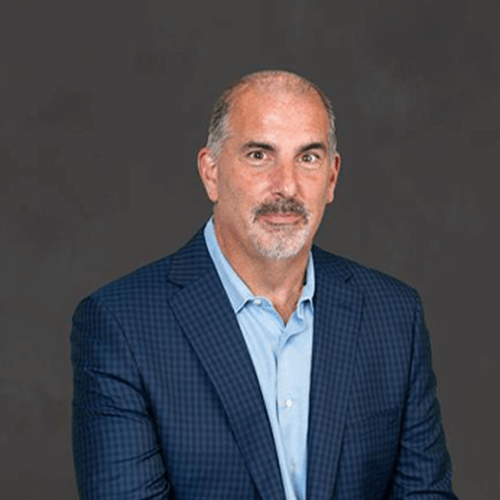
Mitchell Sklar
Director of Mfg Quality, Certification & Product Innovation Director of Prefabrication Strategic Ventures & Market Strategies
ReSIA Manufacturing, LLC
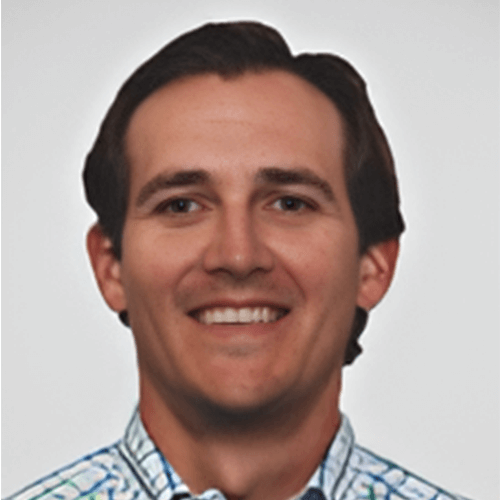
Matt Slataper
President
Ramtech Building Systems, Inc.
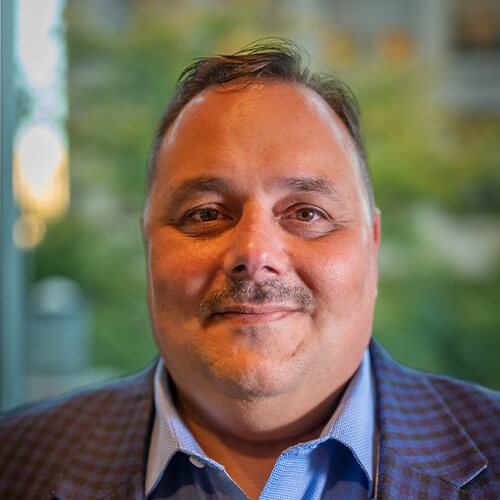
Jon Hannah Spacagna
Government Affairs Director
Modular Building Institute
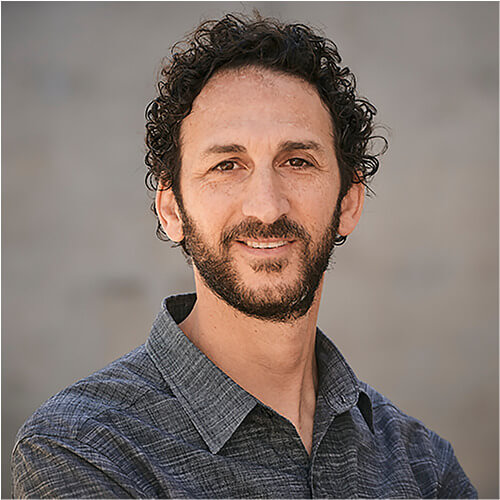
Brian Stark
Co-Founder & CEO
STEEL + SPARK
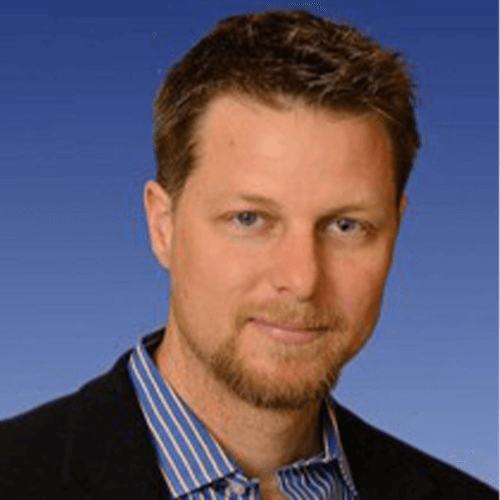
Colby Swanson
Managing Partner
Momentum Innovation Group
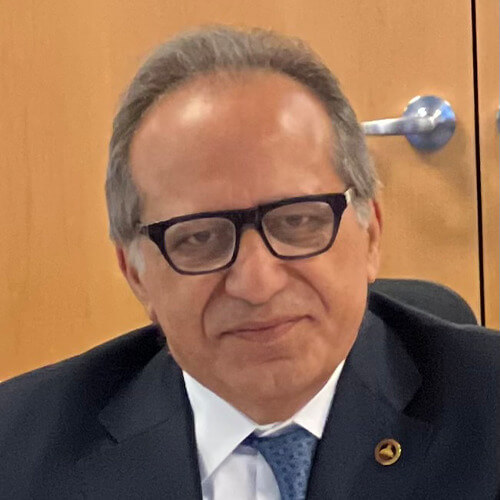
Fuad Sweiss
Founder
Hospitals Without Borders
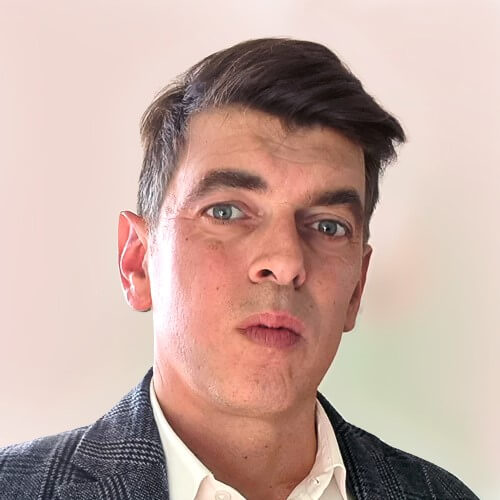
Emanuele Tafuro
Director of Operations
R.I Group
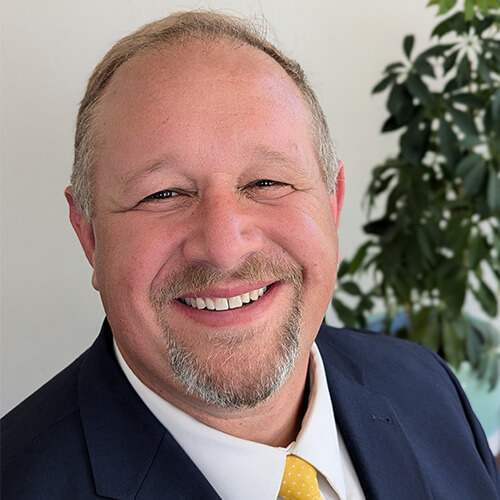
Kam Valgardson
General Manager
Irontown Modular
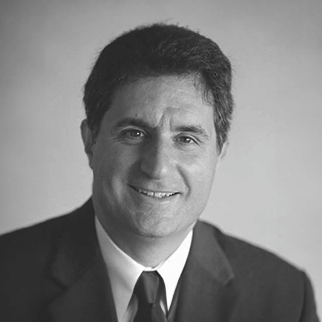
Salvatore Verrastro
Principal
Spillman Farmer Architects
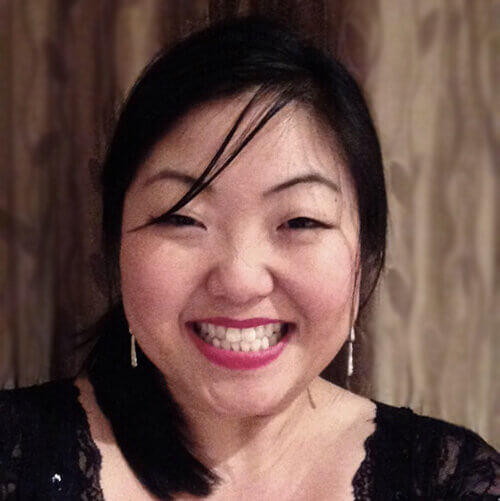
Heather Wallace
Communications Director
Momentum Innovation Group
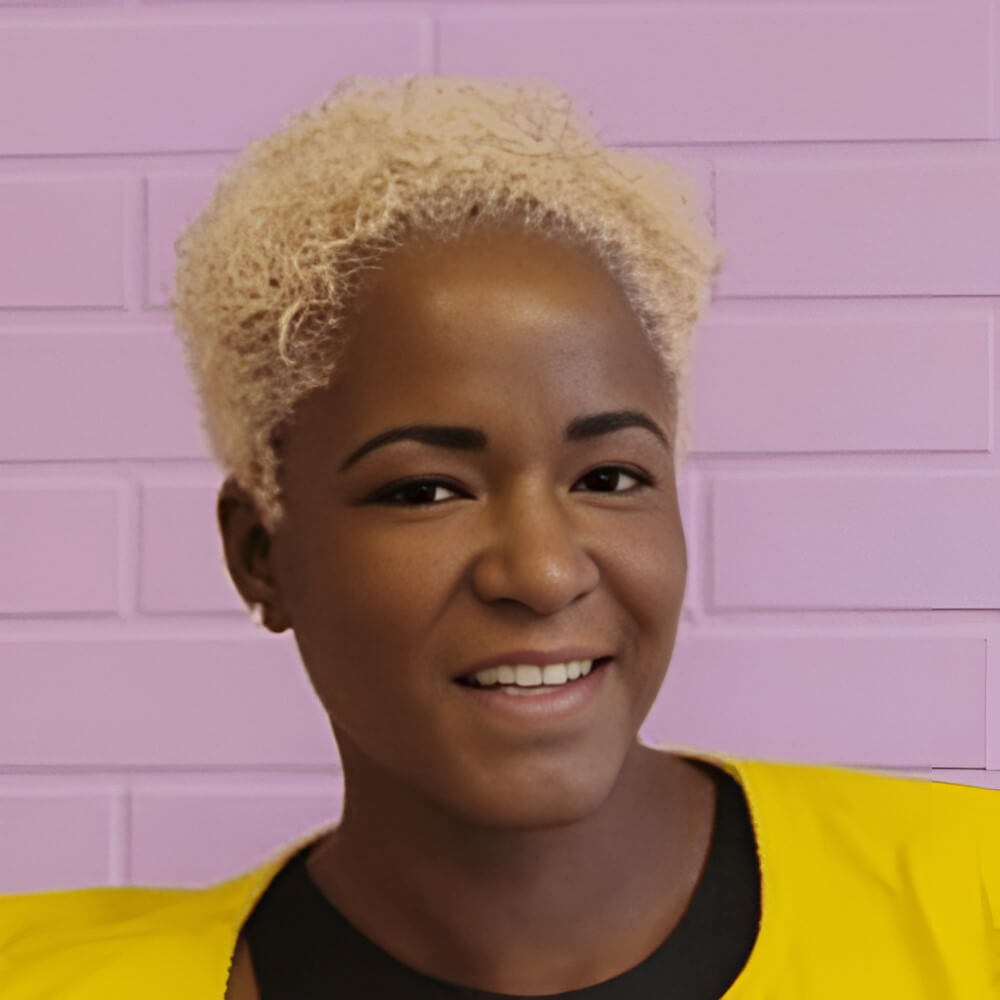
Joan Webley
R.I. Group
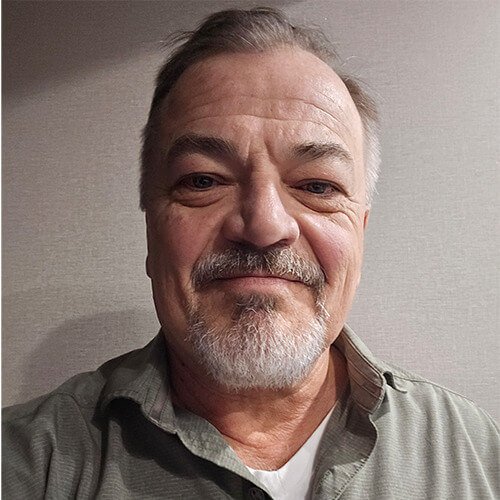
John Westfall
District Representative
CA Department of Housing and Community Development
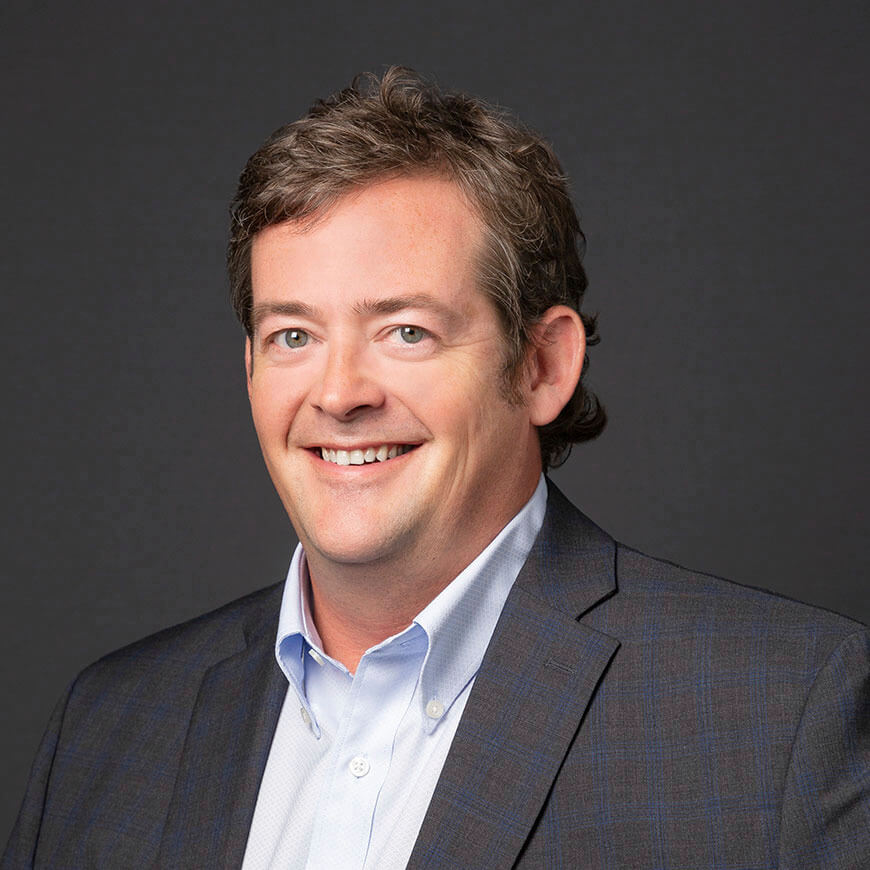
Matt Winter
Director of Mixed Use
LPA Design Studios